トヨタ紡織は,アオイ科フヨウ属の植物であるケナフを射出成形して自動車の内装部品を造る技術の開発に取り組んでいる。目指すのは,ポリプロピレン(PP)の代替だ。
この技術では,直径が5mmぐらいになるまでケナフを粉砕してから,PPの粉末などと混ぜてコンパウンドとし,そのコンパウンドから射出成形材料となるペレットを造る。このペレットを使い,PPと同じように射出成形を行う。ケナフ/PPの射出成形品は,PP単体の射出成形品に対し,剛性に優れる,成形後の収縮率が小さいといった特徴があるという(図)。
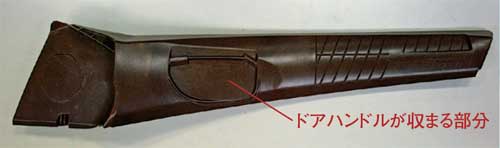
射出成形において,ケナフを強度や耐熱性を高めるための「強化繊維」として機能させている事例は従来もある。だが,それらの事例ではベース材料の割合が多く,ケナフはあくまで「従」の立場だった。トヨタ紡織が開発した技術では,ケナフを「主」にできるのがポイントだ。図に示した試作品におけるケナフと PPの混合比は,ケナフが60質量%,PPが40質量%と,ケナフの方が多い。
相溶化で流動性を高める
その際の問題は,ケナフの流動性である。ケナフの成分は繊維質(主にセルロース)なので,細かく粉砕したぐらいでは「型内で流れない」(同社バイオ技術開発部部長の森高康氏)。ポイントは,コンパウンドを造る段階でケナフとPPを均一に分散させ,相溶化した状態にすることだ。それによって,PPがケナフを運ぶ媒介としての役割を果たすので,PPに匹敵する流動性が得られるという。前述のように媒介であるPPの方が少なくても,媒介としての役割は果たせている。
トヨタ紡織がこの技術の開発に乗り出した背景には,同社特有の“事情”がある。同社はもともと,ケナフを表皮材やプラスチックの強化繊維として使ってきた。例えば,ケナフ表皮材のサイドドアトリム(ドアインナーパネルのカバー)基材は,トヨタ自動車の「レクサス」ブランドの車種を中心に多数採用されている。ケナフを安定調達するために,インドネシアで現地企業と一緒にケナフの栽培に取り組むほど力を注いでいる事業だ。
ところが,昨今の経済環境の悪化に伴う「小型車シフト」により,トリム基材を使うような高級車の売れ行きが落ちており,ケナフ事業に暗雲が立ち込めつつある。小型車のサイドドアは,トリム基材を使わず,PPの射出成形品をむき出しで(特にカバーなどを付けずに)使うことが多い。そこで,PPの射出成形品を代替できれば,ケナフの用途を維持できるという発想の下,新技術の開発に取り組んだ。
同社がケナフにこだわるのは,工業用材料にするまでのプロセスに使うエネルギが,ほかのバイオプラよりも少なくて済むからである。多くのバイオプラでは,でんぷんを分解して糖とし,糖を発酵させてアルコールや乳酸を得て,最終的に所望のポリマを合成する。一方,ケナフはこうしたプロセスを経ず,細かく粉砕して繊維やペレットにするだけである。その点でケナフには優位性があると同社では考えている。
本シリーズは,日経ものづくり2009年8月号特集「こんなに使えるバイオプラのすべて」(pp.36-61)を大幅に加筆・修正したものです。(記事は同特集執筆時の情報に基づいており,現在では異なる場合があります)