
進化したコラボレーションの姿
|
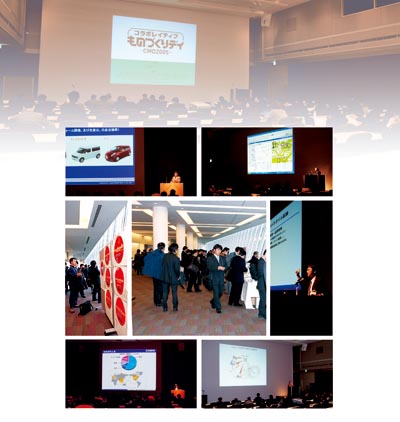
部門間・拠点間・企業間のコラボレーションはどうあるべきか。 単に前工程から後工程へ情報を伝えるだけでなく, 同時並行で情報をやりとりしながら作業を進めることは, 日本企業の得意な「擦り合わせ」の実践に他ならない。 さまざまな形で進む,コラボレーションの最新の姿を紹介する。
日産車体
究極の目標は設計変更“0”の世界
日産車体は,開発・生産準備プロセスの革新を継続している。より一層の品質向上を図るとともに,開発費の低減と開発期間の短縮を狙い,実車による試作回数の削減を図ってきた。
1997年型の「エルグランド」では,実車による試作の回数は,開発試作(試作用の金型を使った試作)が1回,工場試作(量産用の金型を使った試作)が2回の合計3回。それを2002年型のエルグランドでは工場試作のみの2回に,さらに2005年型のコンパクトカー「ノート」では工場試作のみの1回まで減らしている。
実車による試作を工場試作のみの1回にするには,開発品質を向上し,同試作後の設計変更を減らしていくことが不可欠である。そこで「設計変更“0”の世界の実現」を究極の目標としてプロセス改革を進めている。そのためのメインツールが3次元CAD。それを利用した全員参画型のコラボレーションによって開発品質の向上を狙っている。
ヤマハ発動機
イントラネットで部品表と図面をグローバルに共有
ヤマハ発動機は,海外拠点を結んでグローバルに設計部品表を共有するシステム「New-BASE」と,図面を共有するシステム「G-APOLO」を構築した。全世界の25カ所の拠点から部品表を参照できるシステムだ。また,両者を連携させ,部品表の情報から図面を検索できるようにしている。
同社は海外の事業比率が大きく,売上高の内訳は北米27.6%,欧州27.9%,アジア(日本以外)24.7%,日本11.6%(2004年12月期)。基本的には日本の本社で開発したモデルをベースに,各地域で設計・デザインを修正して製品を開発,さらに現地の複数工場で生産,出荷する。
例えば本社で開発したASEAN共通モデルをベースに,タイやインドネシアといった各国に応じた派生モデルを,ASEAN地域の開発拠点独自で開発するといった例がある。道路事情や,二輪車の用途,顧客の年齢や性別の構成,デザインに対する感覚などが国ごとに異なるためだ。
カシオ計算機
在庫指標の社内統一でSCMを再構築
「第1次SCMがあるから第2次SCMがある」(安西仁氏)—一度SCMシステムの運用に失敗したカシオ計算機は,その失敗を糧に再度SCMシステム構築に取り組んでいる。
同社は,1999年に計画立案業務の改革を支援するツールとして,米i2 Technologies社のシステムを稼働させた。これが「ビジネススピードを飛躍的にあげる」「見える・コントロールできる仕組み」をキャッチフレーズにスタートした第1次SCMだ。電卓,楽器,時計の各事業を対象に,需要予測精度の向上やリードタイムの短縮などを図り,在庫削減に取り組んだ。
しかし,週次化を狙っていた計画サイクルは2週次までしか短期化できず,在庫もSCM稼働直後には逆に増大。その後の在庫水準も目標の2カ月には程遠かった。
計算処理に時間がかかることもさることながら,最大の問題は,全体最適を図るという意識が現場に浸透しなかったことにある。生産部門は出荷精度を高めるため在庫を持ったまま運用,資材部門は資材在庫を増やさないよう発注を抑え,営業部門は欠品しないよう計画を上乗せする—といった具合にそれぞれが自部門の都合だけで運用してしまった。これでは,適正な計画を算出できない。
日立製作所
インターネット経由でいつでも,どこでも打ち合わせ
日立グループがコラボレーション環境を構築するに当たって目指したのは,実務担当者が「使いたいときに」「いつでも」「どこでも」「どんなデータでも」「安全に」打ち合わせできることだ。この考えに基づいて同グループは2003年,「Collaborative Meeting@Internet」(以下,CoMet)と呼ばれる実務者用会議システムを構築した。現在では20以上の事業所・関連会社で使われている。
同システムを構築する以前から,日立グループのネットワーク基盤は統一されており,電子メールや事業所ごとに構築したPDMシステムによって非同期の情報共有を実現していた。また,テレビ会議や電話会議といった同期型のシステムも構築してあったが,会議資料が紙のままであるなどデジタル情報の活用が不十分だったことに加え,実務担当者用のツールの数が不足していたために場所や時間が限定されていたのが実情だった。
そこで構築したのが,インターネット経由で使えるASP(アプリケーション・サービス・プロバイダ)方式のCoMetである。ユーザー部門において必要な設備は,インターネットに接続可能なWindowsパソコンのみ。クライアントソフトやビューワ,CADデータの変換ソフトはWebから自動的にダウンロードされ,インストールされる。
パイオニア
2年で実現したグローバルSCM
パイオニアの「P-Project」は,全事業を網羅し,しかも日本,中国,北米,欧州,中東などグループ全体をカバーするグローバルなSCMシステムを構築しようというプロジェクト。利益構造の変革によるフリーキャッシュの創出と連結在庫の削減を狙い,2002年からスタートした。開始から2年余りでシステム構築や製販計画の週次化といった改革の基盤を整え,これから成果の刈り取り期に入ろうとしている。
短期間で多様な事業に対応するために,事業ごとにサプライチェーンのパターンを分類。SCM構築プロジェクトの進め方や仕組みで共通化できる部分と,事業ごとに付加すべき部分の整理から始めた。例えば,車載CDプレーヤーなどは,価格が低めで革新性も低い「普及型商品」,カーナビは,価格も革新性も高い「市場創造型商品」,車載スピーカーは,価格・革新性は低いが商品寿命が長い「安定供給型商品」といった具合。市販のSCMソフトを導入しながら,追加要件の開発でこうした特性を考慮した。
問題は,これを各事業部門にいかに展開するかということ。プロジェクトは専任者が数十人,関連する担当者が数百人に及ぶ。全体最適を目指しながらこの大きなプロジェクトを進めるのが難しい。
日本ビクター
XMLでマニュアル構築,設計情報も連携
日本ビクターが運用している電子マニュアルシステム「XMLサービスマニュアル」は,保守や修理に当たるサービス員に必要な情報を素早く供給することで,復旧までの時間短縮を狙ったシステム。システムの名前にあるようにXMLをベースとしている。
特徴は,単にこれまでの紙の書類を電子化して提供しているのではなく,CADデータを含めて必要なデータはすべてXMLで表現した上で,必要に応じて連携し直して表示していること。これによって,本来必要な情報が得られなかったり,逆に不必要な情報が付いてきたりといったことを防げる。また,使用目的に応じて自分好みにユーザー・インタフェースをカスタマイズすることで,サービス員は自分に最適なマニュアルをオンラインで入手できることになる。
システムを構築した背景には,これまではあまり役立たない電子データをサービス員に提供し続けていたという反省がある。日本ビクターが主に手掛ける情報家電業界では,これまでも例えばPDF形式のファイルなどでマニュアルを提供してきた。
しかし,ほとんど使用されていなかった。理由は大きく分けて二つ。一つは目的とする情報にたどり着くまでに,検索キーの入力など煩雑な処理を繰り返し実行する必要のあること。関連する情報のリンクが満足に整備されていないため,一度目的とする情報を探せても,また次の情報を探すために検索を繰り返さなくてはならない。
大阪ガス
製造履歴の蓄積,分析を品質向上に結び付ける
ガス警報機は,万が一ガスが漏れたときに最後のとりでとなる製品。それだけに誤動作や動作不良などを決して起こさない,高い信頼性が必要だ。
この信頼性をより高めるべく,大阪ガスはメーカーと共同でトレーサビリティー・システムを構築した。トレーサビリティー・システムにより,製品1台ごとの製造履歴を詳細に管理。回収した製品の性能変動度合いと,製造履歴を照らし合わせて分析することで,より信頼性を高めた製品の開発に結び付ける狙いだ。
トレーサビリティー・システムは,トラブル対策やリコール対策に有効な手段と考えられている。市場で不具合が発生したとき,製造履歴をたどれば原因を特定しやすい。さらには,同様の不具合を発生しやすい製品が特定でき,それを顧客に迅速に告知できる。
大阪ガスが構築したシステムも,もちろんこのような使い方ができ,不具合原因を特定できれば,24時間以内に同等の製品を探し出せる。
しかし,大阪ガスでは保証期間内の性能維持には絶対の自信を持っており,このような使い方はあまり想定していない。メインの目的は前述したように,さらなる信頼性の向上にある。性能には自信があっても,実際に長時間稼働し続ければ若干性能は変動する。このとき,蓄積した履歴情報を分析して性能が変動した原因を特定できれば,次期製品はさらに信頼性を高めることが可能だ。