事例分析
トンボ鉛筆【製品力UP・開発力UP】
3Dプリンタで膨大な試作
使いやすさを徹底的に刷新
トンボ鉛筆が2013年3月に発売した修正テープ「MONO ergo(モノエルゴ)」(図1)*1。金沢大学教授の柴田克之氏と共同開発した製品で、使いやすさを人間工学(エルゴノミクス)の点から突き詰めた。その形状決定のプロセスでは、試作が大きな役割を果した。
まず発泡ポリスチレン(以下、発泡スチロール)製の試作品を手作業で削り出して形を調整した後、それをベースに3Dプリンタで実験用の試作品を造形するという2段構えの方法を用いた。これを何度も繰り返す中で膨大な試作品を検証し、製品力を向上させだのだ。
最初の形状をどう生み出すか
MONO ergoの開発プロジェクトは、「修正テープの存在は知っていても、『うまく力が入らない』『狙った場所をうまく消せない』という消費者が一定割合で存在している」(トンボ鉛筆商品企画部プランニング1グループ担当課長の志水秀雄氏)という現状認識から立ち上がった。このようなユーザーの不満の声に応えるために、人間工学を適用して科学的に使いやすさを高めることを開発目標に掲げた。
ところが、プロジェクトの「最初の一歩、つまり、たたき台となる形状を出すところでいきなりつまずいた」(同氏)。既存製品による使いやすさの評価はすぐに実施でき、使いやすさを左右する要素の抽出もできたが、どのような形状にすればその要素を満足できるかが分からない。その最初の形状案をなかなか出せなかったのだ。
〔以下、日経ものづくり2013年10月号に掲載〕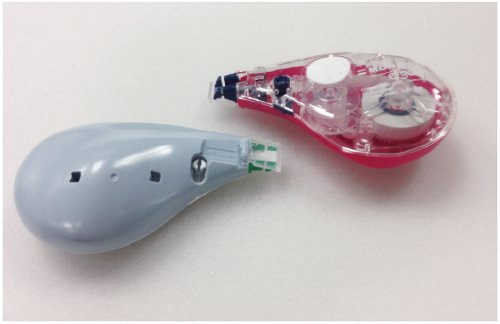
*1 価格は300円(税別)。詰め替え用のカートリッジは180円(同)
ライオン【製品力UP・開発力UP】
一歩先行く検証を掌中に
液体の出し入れ感にこだわる
洗剤などの容器を開発するライオンの包装技術研究所。10数年前は試作品による検証は行っておらず、「2000年ごろから試作品による評価が始まった」(ライオン研究開発本部包装技術研究所副主席研究員の中川敦仁氏)。動向分析でも紹介した通り、試作の数は年々増加している。そんな同社が、どう試作を活用して製品力や開発力を向上させているかを見てみよう。
一昔前は木型1つ
ライオンでは従来、「試作品といえば、製造メーカーに渡す木型くらいだった」(中川氏)。容器の製造は専門メーカーに依頼しており、設計情報としてCADデータと2D図面の他、参照用の木型を作製して渡していた。これらを使って先方で正式な図面を起こし、ライオン側で承認するというプロセスだ。要するに、試作品と言っても設計案の検証ではなく情報伝達を目的としたものだった。
製品の評価は基本的に全てデジタルデータ上で行っていた。ただし、データで評価できるのは強度や内容量といった、形状と物性などから計算できるもの。最終的に木型を作製するので外観形状は実物として確認できるが、木型の重さやさわり心地などは製品と異なるし、この段階で問題が見つかっても大幅な修正はできなかった。
このようなプロセスに変化が生じて開発段階での試作を開始したのが2000年ごろのことである。まず導入したのが、ローランド ディー.ジー.の切削加工機「MODELA MDX」とC&GシステムズのCAMソフト「Craft MILL」だ。これらを利用し、ケミカルウッド(ポリウレタン)を切削加工することによる試作を開始した(図1)
〔以下、日経ものづくり2013年10月号に掲載〕