挑戦・複合材料編
CFRP 【東京R&Dコンポジット工業】
表面粗さRa0.4μmの切削面
剥離も繊維の残りもない
炭素繊維強化樹脂(CFRP)は、炭素繊維にエポキシ樹脂を含浸させたシート(プリプレグ)を何層にも重ねて加熱・加圧して造る。そのため切削時に問題となるのが、プリプレグの間や繊維の間に起きる剥離と、炭素繊維層の削り残しである。これらの問題を解決し、主に二輪や四輪向けにCFRP製部品を企画/設計/生産しているのが、東京R&Dコンポジット工業(本社東京)だ(図1)。
CFRP部品への需要はこれまで、フォーミュラ1(F1)やMotoGPといったレース車両向け部品に限られていた。レース車両向けは、部品1種類当たりの必要個数が少ない。そのため高価な治具を作って機械で切削するよりも、人の手で回転工具を用いて切削する方がコスト面で有利だった。同社は15年前からCFRPを機械で切削するノウハウを蓄積してはいたが、活用する先がそれほどなかったのが実情だった。
ところが、「ここ1 ~2年で急に風向きが変わった」(同社製造部部長の白岩一行氏)という。レース用だけではなく、量産タイプの車両にもCFRPが採用され始めたからだ。
〔以下、日経ものづくり2013年8月号に掲載〕
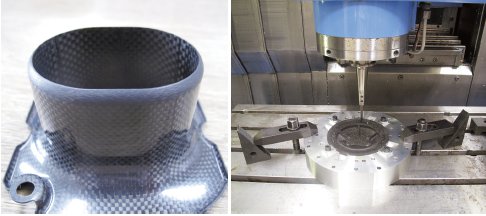
挑戦・樹脂編
ゴム 【扶桑ゴム産業】
柔らかい物を成形よりも短納期で
「切る」と「削る」を使い分ける
高弾性材料、つまり弾性限界が大きいゴムは、金属などと同じように加工しようとしても正確な形状にするのが難しい。通常の切削工具を押し当てても大きく変形して逃げてしまうからだ。そのため、従来は金型を使って成形するのが一般的だった。
そんな中、切削などによるゴム製品の加工を得意とする企業がある。扶桑ゴム産業(本社広島市)だ。天然ゴムや合成ゴム、スポンジのような発泡ゴムまで幅広いゴム材の切削加工技術を持つ。
扶桑ゴム産業はもともと、ゴム製品の商社として創業した。顧客からの特急要求などに対応するために自社内で手作業による加工を手掛けるようになり、一時は自動車メーカー向け成形品の量産がメインの仕事となった。しかし、その受注量の浮き沈みは激しい。そこで、取引先を特定の企業に集中させるのではなく、多くの企業に分散させるために、試作品や小ロット品の加工に目を付けた。「約40年前、旋盤やフライス盤を導入して体制を整えた」(同社代表取締役社長の田村雅春氏)のである。
ゴムの切削加工を可能とすることで、特に少量生産品においてコストや納期などで優位性を発揮できる。例えば、図1(a)に示したゴム足の部品では「500個までならば金型を造るよりもコストは安くなる」(同氏)という。金型が不要なので、納期も当然短い。一般的に金型を作製して成形する場合には納期は約1カ月かかる。これが、ゴムブロックやシート材から削り出す場合には「形状や材質によっても異なるが、納期は2~3日で済む。複雑な形状でも1週間あれば納品できる」(同氏)という。
〔以下、日経ものづくり2013年8月号に掲載〕
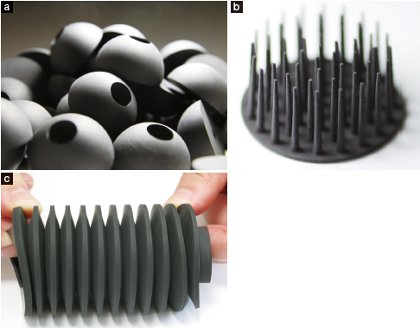
ガラス代替硬質フィルム 【ファインテック】
打ち抜きで加工時間が1/10
理想的な脆性破壊を起こす
「新しいニーズに応える新素材が開発されても、加工に手間やコストがかかってはその良さを生かし切れない。ここに加工技術の出番がある」と、産業用刃物メーカーのファインテック(本社福岡市)代表取締役社長の本木敏彦氏は話す。同社と、フィルムなどの加工メーカーのオーエスピー(同岡山県真庭市)、超硬合金素材を手掛ける冨士ダイス(同東京)などが共同で開発した透明硬質フィルムの打ち抜き加工技術は、まさにその典型例といってよい*。
スマートフォンやタブレット端末の最上面に使われるガラス製表面カバーの代替を狙って、透明硬質フィルムが次々と開発されている。ポリカーボネート(PC)をポリメチル・メタクリレート(PMMA)で挟んだ共押し出しフィルムの表面をハードコートしたものや、有機無機共重合体、光硬化性樹脂といった具合に、さまざまな材料が名乗りを上げている。従来の硬質透明フィルムの鉛筆硬度は2~3H程度だったが、ガラス並みの9Hまで高めた製品も出てきた(図1)。
ガラスと比べた場合の硬質透明フィルムの特徴は、軽くて耐衝撃性に優れること。それ故に、ガラス並みの表面硬さを実現できれば一気に普及する可能性が出てくる。しかし、そこには大きな課題がある。鉛筆硬度が高くなるともろくなり、生産性の高い打ち抜き加工が難しくなるのだ。打ち抜き加工のサイクルタイムは3秒程度だが、レーザ加工で切り出すとその約10倍の30秒程度かかってしまう。当然、製造コストも跳ね上がる。そのため、硬質透明フィルムの打ち抜き加工技術の確立が強く求められている。
〔以下、日経ものづくり2013年8月号に掲載〕
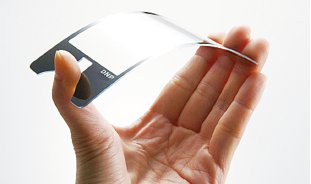
* 「平成23年度戦略的基盤技術高度化支援事業」の1つとして開発を進めた。3社の他、九州大学と金属系材料研究開発センターも開発に加わっている。