ホンダが世界で初めて量産車に採用したハイブリッド・ドア。
コスト上昇を1割程度に抑えつつ、4枚で実に11kgの軽量化を実現。
クルマの軽量化技術の開発が加速する中、ホンダは異なる材料(異材)である鋼とアルミニウム合金を組み合わせたドア(ハイブリッド・ドア)を開発した(上の写真)。北米市場で2013年3月から販売を開始した「Acura」シリーズの新型「RLX」に搭載した(図1)。量産車へのハイブリッド・ドアの適用は世界で初めてとなる*1。
ドアは2枚の板を内外に張り合わせて造る(図2)。このうち、内側の板(インナパネル)に引っ張り強さが270MPaの鋼を、外側の板(アウタパネル)に引っ張り耐力が200MPa以上の6000系(アルミ-マグネシウム-ケイ素系)アルミ合金を採用した。ドアのアウタパネルだけをアルミ合金化することで、両パネルに鋼を使う「オール鋼製」の通常のドアよりも軽く、両パネルにアルミ合金を使う「オールアルミ合金製」ドアよりもコストを抑えることができる。すなわち、ハイブリッド・ドアの特徴は、両タイプのドアの「良いところ取り」だ*2。
事実、新しいハイブリッド・ドアは、クルマ1台当たり(4枚分)でオール鋼製ドアよりも11kg軽量化しながら、コストは10%増し程度と低く抑えることができた。オールアルミ合金製ドアの場合は、オール鋼製ドアよりも22.5kg軽くなるものの、コストが2.9倍にも跳ね上がってしまう。
ハイブリッド・ドアの生産を手掛けるのは、埼玉製作所の狭山工場。まずはRLX向けの量産をこなしつつ技術を構築して、順次他車種へと採用を拡大する計画だ。これに伴い、「グローバル生産の展開も目指す」(本田技術研究所四輪R&Dセンター第10技術開発室第3ブロック研究員の田野口健一氏)という。
コストの大幅な上昇を抑えつつ確実な軽量化効果を生むハイブリッド・ドアの利点は、もちろん、競合メーカーも知っている。そのため、ホンダ以外の自動車メーカーもこれまで開発を進めてきたが、量産車レベルでは実現できていなかった。
熱変形が最大のネック
その理由を、ホンダの田野口氏は「鋼とアルミ合金という性質の異なる材料を結合することで生じる3つの難しい課題を解決することができなかったから」と説明する。具体的には、[1]熱変形を抑える、[2]強固な結合方法を確立する、[3]電食を防止する、という課題である。
中でも、[1]の「熱変形を抑えることに、他の自動車メーカーは苦しんできた」と同氏は言う。というのも、仮に異材であることを無視してオール鋼製ドアと同じように造ると、10mmもの単位で反りやへこみが発生し、建て付けが成立しないほどドアが変形してしまうからだ。
〔以下、日経ものづくり2013年4月号に掲載〕
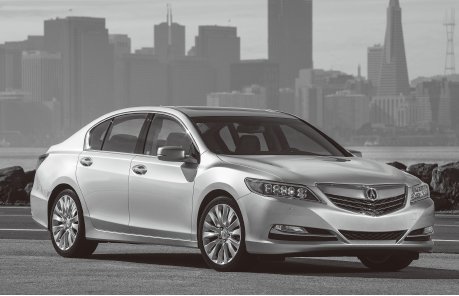
*1:インナパネルにアルミ合金を、アウタパネルに鋼を使う逆の組み合わせのドアの実用化例も無い。最大の理由はコストが高いこと。インナパネルは取り付け部品が多く複雑な構造となる。これに伴う生産技術開発や専用設備が必要となり、製造コストが跳ね上がる。
*2:ドアのアウタパネルをアルミ合金化すると、車両の外側が軽くなって重心が中心に寄る。そのため、操縦安定性が高まるという利点もある。