第1部<変革への決意>
震災を機に壁を打ち破り
世界で戦う体制を整える
震災以降、リスク対応とコスト削減の両立を求められた日本のエレクトロニクス・メーカー。これらの両立に頭を悩ます中で、災害への対策が、競争力の強化につながる可能性が見えてきた。震災を機に、日本のエレクトロニクス・メーカーが大きく変わろうとしている。
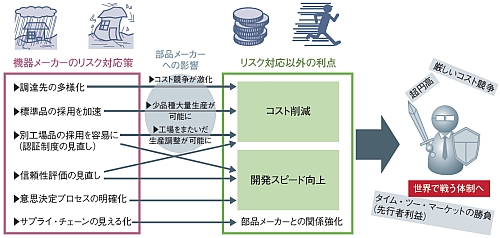
2011年3月11日に発生した東日本大震災。日本の多くのエレクトロニクス・メーカーは、サプライ・チェーンの寸断により大きな被害を受けた。
それから約1年。タイの洪水という新たな脅威に見舞われながらも、二つの災害で露呈した弱点を克服すべく、サプライ・チェーンの強化に挑んできた。
振り返れば現場では、現状把握から始まり、代替部品の確保、短期間での設計変更や信頼性の評価、工場の復旧といった困難を次々と乗り越えてきた。平時とは異なる環境で、多くの技術者が協力しながら知恵を絞り、製品の供給を何とか続けてきたのだ。
これらの経験は、決して無駄ではなかった。個々の技術者の危機対応力を高めると同時に、日本のエレクトロニクス・メーカーの姿を大きく変える起爆剤になろうとしている。災害からの復旧の先に、国内メーカーの新たなステージが待っている。
リスクとコストへの認識が変化
国内エレクトロニクス・メーカーの災害リスク対応に関する考え方は、震災前と震災直後、さらには震災から1年を経て大きく変化してきた。震災前は、災害リスク対応はコスト増加要因であり、厳しいコスト競争に逆行するという認識が支配的だった。例えば在庫を増やしたり、生産拠点を二重化したりすることは、コスト増に直結するため認められないという考え方だ。
震災直後は、世界からの厳しい視線を受けて、コストが増えても災害対応を進めざるを得ないという考え方に変わった。「BCP(事業継続計画)」の名の下に、在庫を持ったり、生産拠点を二重化したりするのは、もはや当たり前となった。ただし、コスト増分を誰が負担するかについては、結論が出ていなかった。
そして震災から1年を経て、災害リスク対応とコストの削減などは両立できるという考え方が徐々に広がりつつある。
第2部<部品メーカーの対策>
リスク情報を顧客と共有
災害時も供給を切らさない
製造リードタイムの長い半導体は、機器に搭載する部品の中でも特に災害時のリスクが高い。半導体メーカーはリスク情報を顧客と共有することで、災害時にも製品を供給し続けられる体制を構築しようとしている。
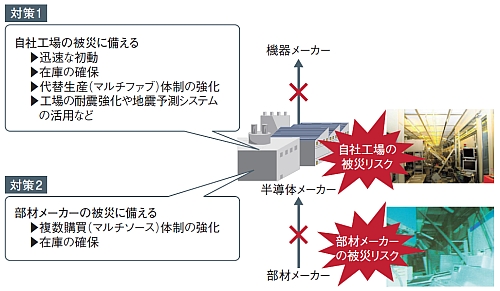
「自動車メーカーにとって、半導体ほどリスクの高い部品はない。製造に3カ月もかかる部品なんて、他にないからだ」──。
自動車メーカー出身で、現在はフリースケール・セミコンダクタの車載半導体を担当しているある技術者は、半導体の特殊性をこう指摘する。実際、東日本大震災やタイ洪水では製造リードタイムの長い半導体において深刻な供給不足が発生し、機器メーカーや自動車メーカーに大きなダメージを与えてしまった。その苦い経験をバネに、半導体メーカーは今、災害に強い供給体制の構築に全力を注いでいる。
主な対策は二つある。一つは自社工場が被災した場合への対策、もう一つは部材メーカーが被災した場合への備えである。
迅速な初動で被害を最小化
自社工場が被災した場合、迅速な初動によって被害を最小限に抑えるとともに、一刻も早く顧客に復旧計画を提示することが重要となる。さらに復旧までの間、在庫と代替生産によって供給をつながなくてはならない。今後の災害に備えた工場の耐震強化も必要となる。以下では、こうした対策について、半導体メーカーの取り組みを紹介する。
第3部<タイ現地報告>
洪水をきっかけに
理想の生産ラインを作る
タイには、主要な工業団地だけでも450社以上の日系企業が集まっている。そのタイを襲った洪水が発生してから約5カ月が経過した現在も、地道な復旧作業が続く。現地では、洪水リスク対策とともに、新たな工夫を盛り込んだ生産ラインの構築が始まっている。
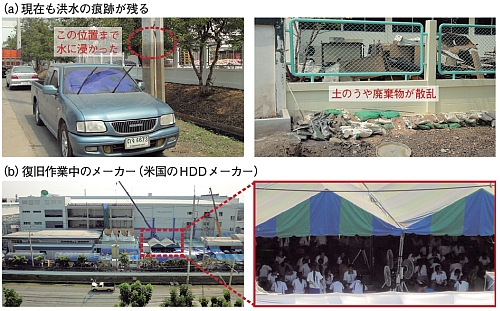
「2月にこんなに暑いのは異常だ。1月にも珍しく雨が降った。今年も洪水に見舞われるのではないか」──。タイの日系メーカーの工場に勤める複数の日本人従業員は、洪水の再来を口々に心配する。実際、工場の復旧をあきらめてタイからの撤退を決めたり、タイ国内で洪水被害を受けたことのない場所に移転する例も出てきている。
しかし多くのメーカーが、洪水を心配しながらも、被災した工場の復旧に取り組んでいる。それは、「教育すれば非常に優秀になる」(日系電子部品メーカーの元タイ工場長)という人材を手放さないためである。そうした可能性のある人材は、今回の洪水被害を受けた「アユタヤからバンコクにかけての地域に多い」(日本メクトロンの現地工場の関係者)ことも、工場の移転を難しくしている。
タイの日系メーカーは今、洪水リスクのある被災工場の復旧に当たって、洪水対策をどのように盛り込んでいくのかに頭を悩ませている。
1階には移動できる装置のみ
今回のタイの洪水では、2011年10月上旬から主要な工業団地への浸水が始まった。排水が完了した11月中旬~12月上旬に復旧作業が始まり、その後、生産の一部が再開されている。
2012年2月下旬に現地を訪れると、多くの工場はペンキを塗り直すなどして外観をきれいに整えており、洪水があったことを感じさせなかった。しかし、電柱には水に浸かった痕跡が残り、土のうや廃棄物が散乱している工場が見られた。工場の中をのぞくと、装置の洗浄といった復旧初期段階とみられる作業を続けているメーカーもあった。