今夏、多くの工場で商用電力の消費が大幅に制限される。その率、前年実績の15%。とりわけ以前から省エネルギ化を進めてきた工場には、15%という数字は重くのし掛かる。効果が大きいのは自家発電や夜間操業といった手段だが、これらに頼りすぎては競争力が落ちる。今夏以降も同様の電力制限を受ける可能性がある。将来を見据え、エネルギの消費効率を改善しなければならない。苦しい環境下、緊急対応と体質強化の両立に挑む工場の節電事例を紹介する。(高野 敦、高田憲一)
一時しのぎで終わらせない、体質強化の原動力に
前代未聞の夏が始まる。前年までほぼ自由に使えていた商用電力が、今年は大幅に不足しているのだ。
東日本大震災の影響により、電力会社の供給能力は低下した。仮に供給が需要を下回れば、電力会社の管内で大規模な停電を引き起こす恐れがある。こうした事態を回避するため、政府や電力各社は需要家に節電を要請している。
そのうち東京電力および東北電力の管内では、電気事業法第27条に基づく電力の使用制限が2011年7月1日に発動される。期間は、東北電力管内が同年9月9日まで、東京電力管内が同月22日まで。制限率は、原則として2010年の最大消費電力の15%である。契約電力が500kW以上の「大口需要家」に対しては法的な拘束力があり、故意に制限を超えて電力を使った場合は罰金の対象となる。工場の多くは大口需要家に相当するので、15%の節電は必達目標だ。
両社以外では、関西電力が一律15%の節電を全ての需要家に要請した他、中部電力や北陸電力も数値目標を設定しない形での節電を呼び掛けた。これら電力会社の管内においても、強制力は伴わないが、節電が求められることになる。
〔以下、日経ものづくり2011年7月号に掲載〕
戦略1:ジェイテクト 東京工場
熱処理工程を徹底攻略
自動車や建設機械などの部品を造っているジェイテクトの東京工場(東京都羽村市)では、2011年夏の最大消費電力(ピーク電力)を前年の実績から25%削減できる見通しを得た。東京電力管内にある同工場に課せられた削減率は15%。差分は、電力の削減が難しい他拠点の支援に回す。
同工場で節電が進むきっかけになったのは、東京電力管内で2011年3月に実施された計画停電。「あの期間は、生産ラインの操業を止めるしかなかった。この停電で危機意識が芽生えた」(ジェイテクト東京工場長の厚海敏幸氏)。春先の段階で電力が足りないのなら、需要がもっと増える真夏は一体どうなるのか。その時点で使用制限の制限率は決まっていなかったが、最悪の場合を想定して独自に電力30%削減という高い目標を据え、対策を講じてきた。それが功を奏し、15%を大幅に上回る方策を積み上げたのだ。
〔以下、日経ものづくり2011年7月号に掲載〕
戦略2:荒川樹脂 つくば工場
射出成形機の断熱で2重の効果
荒川樹脂(本社東京)のつくば工場(茨城県つくばみらい市)は、もともと節電に力を入れている工場だ。同工場の主な生産品目は、注射器をはじめ、CT(コンピュータ断層撮影装置)向け造影剤の容器といった医療用容器や、半導体の製造で使う容器類(図1)。こうした製品には高度な清浄度が求められるので、31台の射出成形機全てをクリーンルーム内に設置して生産している。
つくば工場のクリーンルームは、取り入れた外気を22~23℃に調整して室内を空調し、空気の清浄度(ホコリの数が1万~10万個/m3)を保つために循環させずに排出している。室内の空気は1時間で10数回も入れ替わるので、一般的な空調に比べて桁違いの電力を消費する。
しかも、樹脂を溶かして成形する射出成形機は巨大な発熱体なので、空調に対する負荷が高い。特に夏期は工場の消費電力の半分以上がクリーンルームの電力代に消えており、通年で見ても生産コストの2~3割を占めるという。このため、クリーンルームの節電はコスト削減に直結するので、常に最優先課題だったのである。
〔以下、日経ものづくり2011年7月号に掲載〕
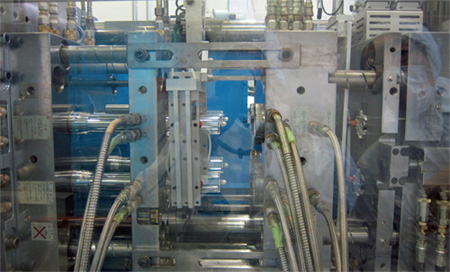
戦略3:キユーピー 五霞工場
常識破りの「窓」多用
マヨネーズやサラダドレッシングを生産するキユーピーの五霞工場(茨城県・五霞町)では、2011年夏のピーク電力を前年から25%以上削減する方針だ。2011年6月上旬時点で、前年実績の約4000kWに対して1100kW(約28%)の電力削減にメドを付けた。
使用制限率(15%)を超えた分は、他の事業所に回す。同工場は、東京電力管内のキユーピーグループの事業所としては消費電力が最も多い。同工場で節電が進めば、グループ全体では余裕が生まれる。「グループの中には15%の電力削減が厳しい事業所もある。減らせるところでなるべく減らさなければならない」(同社五霞工場生産技術課課長の越川孝男氏)。
節電方策の内訳を見ると、同工場も「操業時間を夜間に変更」「発電機の活用」といった「守りの節電」による効果が大きい(図2)。だが、これらはpp.40-41で指摘した通り、従業員の労務環境やコストなどに深刻な影響を及ぼす。そこで「攻めの節電」の比率を高めるべく、省エネルギ化を現在も進めている。
〔以下、日経ものづくり2011年7月号に掲載〕
戦略4:アスモ 本社工場
投資ゼロでコージェネ大改造
自動車用モータの大手であるアスモ(本社静岡県湖西市)の本社工場が取り組んだのは、コージェネレーション・システムの大改造である。電力や熱を直接造り出す設備の効率化は、波及効果が大きく一般性も高い。同工場は中部電力の管内に立地し、改造したコージェネシステムが稼働したのも2009年4月なので、2011年夏期に向けた対策ではないが、今後の攻めの節電のために参考なる。この後に続く3つの事例も今夏のための対策ではないが、やはり攻めの節電という視点から重要なので紹介していく。
改造の目的は、熱を使い切ること(図3)。コージェネシステムは電力だけではなく、発電の際に発生する熱を有効利用することでエネルギ効率を大幅に高められる。そのため、熱の使用量が多い食品工場などで普及が進んでいる。一方、組み立てや加工などの製造業の工場では熱需要が少ないので、活用が難しい。実はアスモも、後述するように熱の利用で課題を抱えていた。
しかし、2008年に実施した設備の改造や更新、新設などの改良工事によって、その課題を一気に解決した。そして、改造前と比較して工場の全消費エネルギの約9%に当たる8000MWh/年の電力と、同じく約3.5%の3300MWh/年に相当する天然ガスを減らした。合計すると約12.5%の節電である。しかも、ESCO事業として実施したため、アスモの改造工事への投資額はゼロだ。
〔以下、日経ものづくり2011年7月号に掲載〕
戦略5:日立電線 高砂工場
クリーンルームには我慢させる
大量の電力を使うクリーンルーム。日立電線の高砂工場(茨城県日立市)は、そのクリーンルームの空調の消費電力を約30%削減した。カギは、冷凍機の制御にある。
同工場は、電線や無線システム関連製品、化合物半導体など、幅広い製品を造っている。その中で、化合物半導体は生産ラインの敷地面積は小さいものの、消費電力は工場全体の半分以上を占めている(図4)。この化合物半導体の製造工程の消費電力をいかに下げるかは、恒常的に抱えていた課題だった。
クリーンルームの単位面積当たりのエネルギ消費量は「一般的なラインの3~4倍」(同社産業インフラ事業本部生産技術部主管技師、建設・空調・省エネルギー技術管掌の田代完二氏)に達するという。その大部分は、空調のための電力である。クリーンルームで造る製品は温度条件が厳しいことが多い上、温度を常に一定に保たなければならないからだ。逆にいえば、空調の効率を改善できれば、消費電力を大幅に削減することが可能になる。
〔以下、日経ものづくり2011年7月号に掲載〕
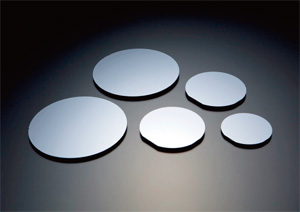
戦略6:OKI 富岡工場
チラーは外に持っていく
OKIの富岡工場(群馬県富岡市)では、チラーの設置場所を変えることで夏と冬の空調効率を大幅に改善した。従来は屋内に置いていたチラーを屋外に移設したのだ(図5)。
このチラーは、レーザ加工機の発振器部分を冷やすためのもの。単に移設しただけといえばそうなのだが、実はチラーを屋外に置くこと自体が常識に反することだった。同社生産本部製造部部長の山科良宣氏は、チラーを屋外に移設した後でレーザ加工機メーカーの担当者にそのことを伝えたところ、そんなことが可能なのかと逆に聞かれたほどだったという。
〔以下、日経ものづくり2011年7月号に掲載〕
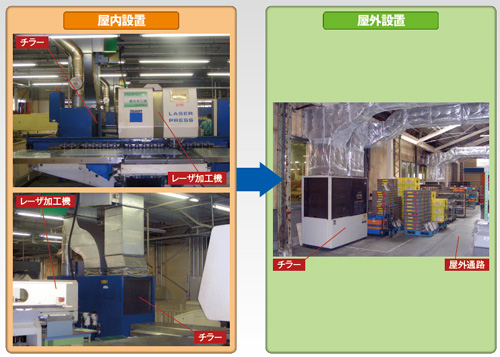
戦略7:横河電機 甲府工場
電力見える化で理詰めの節電
横河電機の甲府工場(甲府市)は、プロセス産業の省エネルギに役立つ制御機器や、計測機器などを生産している。省エネルギ機器の工場だけあって、同社の省エネルギと節電のモデル工場でもある。同社が開発した、見える化でエネルギのムダとりを支援する工場エネルギ管理システム「Enerise E3」もいち早く導入している。
そして、こうしたシステムなどをまず顧客に知ってもらう狙いもあって、甲府工場の省エネ・節電対策を紹介する見学会を実施している。この見学会を担当する横河電機ソリューション営業統括本部VPS開拓本部エネルギーコンサルティング部副部長の石川保郎氏は、最近あることに気付いた。
「見学するお客様が知りたいことは、横河電機のエネルギ管理システムでもなければ、甲府工場の具体的な対策例でもない」(同氏)。エネルギ管理システムは他にもあるし、具体的な対策にしても、業種や業態が違えば通用しないこともある。「それよりも知りたいことは、対策をいかに見つけ出すか、そしていかに実行していくかだ。そして、そのために甲府工場が何を重視しているかを考えていくと、システムと組織にたどり着いた」(同氏)。システムとは、電力計やエネルギ管理システムといった、見える化に関わるもの。一方、組織とは人に関わるものだ。この2つが両輪となって、継続的な省エネ・節電が可能になる。
〔以下、日経ものづくり2011年7月号に掲載〕
アタゴ 深谷工場
働きやすい「省電力工場」
「外光利用と断熱、この2つを徹底した」。アタゴ(本社東京)代表取締役社長の雨宮秀行氏は、同社が埼玉県深谷市に新設した深谷工場をこう説明する。省エネルギ化はもちろん、品質や働きやすさにも配慮したことが特徴だ。
同社は、光の屈折を利用して物質の濃度を計る屈折計のメーカー。果物の糖度計測や調味液の濃度計測といった用途に向け、さまざまな種類の製品を生産している。従来は埼玉県・寄居町の寄居工場が主力拠点だったが、生産量の増加に伴い同工場が手狭になった上、拡張も不可能だったため、新工場建設に踏み切った。2008年のリーマンショックで建設を凍結した時期もあったが、その後も海外市場を中心に市場が拡大しており、建設を続行。2011年4月末から深谷工場で本格的な生産を開始している。
〔以下、日経ものづくり2011年7月号に掲載〕