金属の流れを見極めて工程設計
冷間鍛造の守備範囲を拡大
鍛造やプレス成形といった塑性加工は、切削加工などに比べて工数が少なくて済むため、ある程度の生産量があればコストダウンを期待できるつくり方だ。実現できる精度や形状の複雑さのレベルも向上しており、適用範囲は拡大している。
しかし課題もある。特に、常温で鍛造する冷間鍛造では、塑性変形に伴う加工硬化が最も厄介だ。複雑な形状の場合、最終形状までに焼きなまし(焼鈍)と表面処理(ボンデ処理)を何度も繰り返さなければならないこともある。これらの工数が増えるとコストアップ要因となり、「これで冷間鍛造の適用範囲の限界が決まったりする」〔豊島製作所(本社埼玉県東松山市)代表取締役社長の木本大作氏〕。
逆に言えば、焼鈍とボンデ処理を減らすことが、冷間鍛造の適用範囲の拡大へとつながる。それには、塑性流動を見極め、加工硬化を極力抑えることがポイントとなる。さらに、「冷間鍛造だけにこだわることなく、プレス加工やファイン・ブランキングなど他の塑性加工との組み合わせも考える」(同氏)。すると、今までは使えないと思っていた用途に冷間鍛造を適用し、低コスト化を図れる可能性がでてくる。
圧縮して厚くする
豊島製作所が従来のつくり方を冷間鍛造によって置き換え、低コスト化を実現した例がある。パイプと鍛造品を溶接して造っていた、ある自動車部品だ。従来は溶接部分のリークテストが必要となるため、部品を一体成形したいというニーズがあった。
この部品には、円筒形状の薄肉部分と固定用ボルトを差し込む厚肉部分がある。板金加工では厚肉部分を成形できないし、冷間鍛造では円筒部分のような薄さを実現するのは難しい。同社は試行錯誤を続け、丸棒から冷間鍛造によって一体化した部品を成形することに成功した。
しかし予想通り、焼鈍とボンデ処理の中間処理が何度も必要だった。冷間鍛造において、1工程で素材の断面を減少させられる割合には限界があり、薄肉部分の成形には何工程も必要だったからだ。この点について同社は、板材に冷間鍛造を適用することで焼鈍とボンデ処理を途中に挟み込む必要をなくし、製造コストを大幅に削減している。
板材を絞って、冷間鍛造するという方法はCVT(無段変速機)のハブの成形でも適用した(図1)。このCVTのハブは一見、単純なプレス加工品のように見える。実際、従来は板材を8工程のトランスファープレスで製造していた。
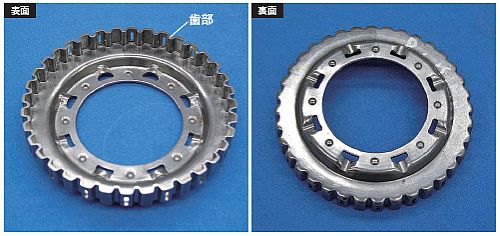
この形状で難しいのは、歯形となっている周辺の折り返した部分。凹凸がある分だけ周長が長くなり、単純に折り返したのでは板厚が薄くなってしまう。従来は、最終形状よりも大きめの直径で折り曲げ、中心に向かって寄せながら成形していくという方法だった。これを同社は、絞り工程で折り返した後、冷間鍛造によって歯部を増肉しながら形成する方法を適用。工数も、ブランク工程も含めて2工程で済むようになり、低コスト化とともに歯部の形状精度を向上した。
成形したい部分は最後まで残す
焼鈍やボンデ処理などの中間処理を大幅に削減した取り組みとしては、円筒の片側をフランジでふさいだような自動車部品がある(図2)。円柱形状の素材から、円筒部分とフランジ部分をそれぞれ別の工程で成形する。
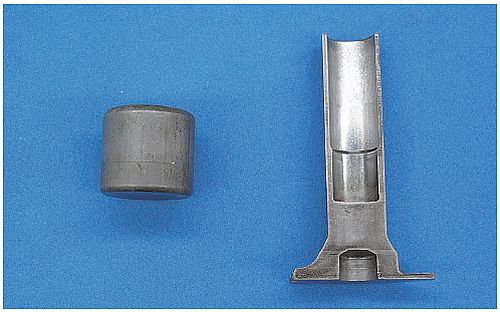
この際、どちらを先にやるのかが大きなポイントだ。従来は円筒部を先に成形し、フランジ部を次に成形していた(図3)。ところが、この順番だとフランジ部の成形で変形させたい部分が加工硬化してしまう。このため、中間処理が必要となった。
そこで同社は、この順番を逆にした。「工程ごとに、変形させたい部分がある。そこに加工硬化が残らないようにする」(豊島製作所の木本氏)ことを考えたのだ。フランジ部を成形する際には、次に円筒部を成形する部分を金型で圧縮しない。これによって、加工硬化が発生せず、中間処理を不要としたのだ。この結果、トランスファー化が可能になり、素材から数十秒で成形が完了する。リードタイムを短縮でき、コストも「3~4割削減できた」(同氏)という。
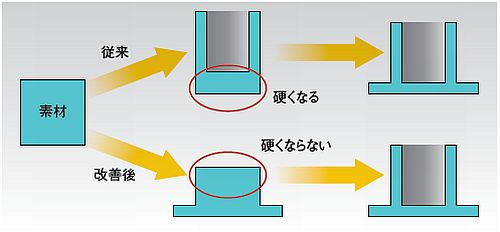
「長い間続けてきた冷間鍛造でさえ、つくり方を工夫する余地はまだまだある。原理原則と実物を大切にするが、従来の成功事例にしばられないことが肝要だ」(同氏)。冷間鍛造というジャンルにも縛られることなく、同社は今後も最適なつくり方を探し続ける。