日本の製造業が得意とする先進的な製品の多くに、レアメタル(レアアースを含む)が使われている。レアメタルだからこそ高い性能を実現できているとの認識は、いつの間にか、レアメタルへの過度な依存状況を作り出した。しかしこの認識は、果たして本当なのだろうか。近年明確になったレアメタル調達リスクの大きさは、「レアメタル依存症」からの脱却を日本の製造業に強く求めている。(中山 力、高田憲一、富岡恒憲)
Part1:依存の実態
いつの間にか不可欠に 利用の根拠に立ち返れ
「ガラスの研磨剤として使われているセリウム(Ce)は、資源量が豊富で安価だから使っていただけという側面がある」。こう指摘するのは、東北大学未来科学技術共同研究センター(NICHe)副センター長の小澤純夫氏だ。ところが、5年間で2倍にも上昇していなかったCeの価格が2010年の夏、約1カ月で4倍に高騰。さらに同年秋には、入手困難な状況に陥った。
一時的とはいえ、Ceの供給が途絶えると、それを使っていたものづくりが大きな危機に曝された。液晶パネルやHDDなどに不可欠なガラスの研磨を手掛ける、ある工場では、「2010年9~11月までCeの輸入が止まったことで研磨剤が入手できなくなった。在庫を吐き出しつつ何とか対応したものの、もしあと1~2カ月輸入停止が続いたら、生産が停止した恐れがあった」。
〔以下、日経ものづくり2011年1月号に掲載〕
Part2:さらば安直使用
研磨剤(Ce)◆視点を変えて装置側からアプローチ
酸化セリウム(CeO2)が主成分の研磨剤は、レアメタル依存症の典型だ。それ故、「削減」「代替」の可能性を示す格好のケースにもなっている。
CeO2研磨剤は、高度な平滑面が求められる液晶ディスプレイやHDD向けガラス基板などの研磨に使われる。以前は酸化鉄(Fe2O3)が使われていたが、研磨能率と、研磨後の平滑性が優れるために、費用対効果はFe2O3よりもむしろ優れている。しかもレアアースでありながら価格は5~6米ドル/kgと安かったため、一気に普及した。CeO2を研磨剤として利用する際、ちゅうちょする理由は何もない。いつしか空気のような存在になっていたのである。
ところが、状況は一変する。中国の輸出規制によって需給が逼迫した。「2010年9月以降、国際価格は約10倍の50米ドル/kg程度に跳ね上がった」(CeO2研磨剤大手の昭和電工)のだ。昭和電工は同月13日、原料高騰に耐え切れずに同研磨剤を約4倍に値上げすると表明した。値上げ幅は3500円/kg以上。その後、中国からの輸入は再開したが、原料価格は高止まったままだ。
2010年9月以降、CeO2代替の可能性を示す技術に注目が集まった。同年6月にファインセラミックスセンターを中心にした研究グループが、同年9月に立命館大学を中心にした研究グループが、代替技術を発表していたからだ。
いずれの研究も今回の中国の規制とは直接関係なく、新エネルギー・産業技術総合開発機構(NEDO)が実施する「希少金属代替材料開発プロジェクト」の一環として進められたものである。成果が公表されたタイミングが中国の輸出規制とほぼ重なったため、がぜん注目が集まった。興味深いのは、両者の研究のアプローチである。例えば、立命館大学のグループが注目したのは研磨剤の主成分である砥粒ではなく、砥粒を保持する研磨パッドの方だった。
〔以下、日経ものづくり2011年1月号に掲載〕
モータ用磁石(Dy)◆メカニズム解明し必要な所に必要なだけ
小型で軽量な高性能モータとして幅広い用途で使われているのが、永久磁石型の同期モータ(PMモータ)である。ハイブリッド車(HEV)や電気自動車(EV)の走行モータをはじめ、電動パワーステアリングの駆動モータ、省エネルギ型のエアコン用圧縮機のモータ、ドラムを斜めに配置した洗濯機のドラム駆動用モータ、工作機械の位置決め/割り出しやロボットに使う産業用モータなどさまざまなところで活用されている(図1)。
ただ、こうした用途向けに高い性能を実現するには、現状では高性能磁石であるネオジム・鉄・ボロン(Nd-Fe-B)系焼結磁石が不可欠。例えば、HEVでは約1kg/台、EVでは約2kg/台のNd-Fe-B系焼結磁石が使われている。その磁石原料としてのNdに加え、高い耐熱性を求められる用途向けにはジスプロシウム(Dy)やテルビウム(Tb)といったレアアースが必要とされる。Dy(または一部をTbに置換)は、HEV/EV用の走行モータの場合でNd-Fe-B系焼結磁石の総質量の7~10質量%、エアコン用圧縮機のモータの場合で4~5質量%添加されている。
〔以下、日経ものづくり2011年1号に掲載〕
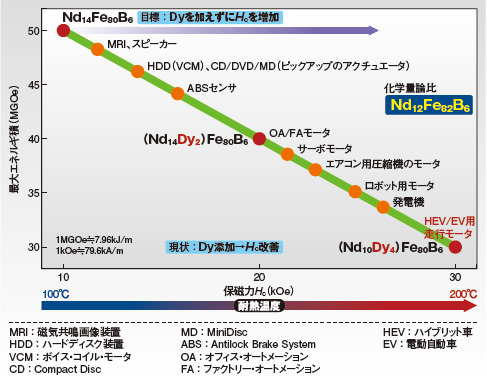
Mg合金(Y/Gd)◆添加剤に頼らずに熱処理で対応
ある特性を高めれば実用化に大きく近づく合金があったとしよう。研究開発の結果、その実現方法が発見されれば、一気に実用化が進むかもしれない。ただし、もしその方法にレアメタルの使用が不可欠だったならば、レアメタルを使わない別の方法の研究にもチャレンジする──。レアメタル依存症からの脱却には、そんな取り組みが必要になる。
その好例が、マグネシウム(Mg)合金の高強度化だ。Mg合金の密度は鉄(Fe)の約1/4とアルミニウム(Al)よりも小さく、地球上での存在量も多い。コスト面での課題は残るものの、次世代の軽量化材料として注目を集めている材料だ。
特に、軽量化が燃費改善と二酸化炭素(CO2)の排出低減に直結する自動車では、Mg合金への期待が高い。実際、ある欧州の自動車メーカーがMg合金を構造材料として使った自動車を試作。その総質量は260kgで、燃費は100km/Lにもなったという。
ただし、自動車用の構造材料としてMg合金の適用を考えた場合、「比強度や破壊靭性値がAl合金と比較して低い」(物質・材料研究機構新構造材料センター軽量材料グループグループリーダーの向井敏司氏)ことが課題だ。現状で一般的なMg合金(AZ31)の鋳造材料では、降伏応力と比重の比である比強度は約120MPa、破壊靭性は20MPa・m1/2。展伸材ではいずれも高くなるが、それでもAl合金には届かない。2000系や7000系のAl合金では比強度が150MPaを超えるし、破壊靱性も30MPa・m1/2を超えるものが多い。
〔以下、日経ものづくり2011年1月号に掲載〕
排ガス触媒(Pt/Pd)◆浄化システムとして捉え全体最適を目指す
自動車排ガス触媒に使う元素は、白金(Pt)やパラジウム(Pd)などの白金族である。価格が高いので、使用量を削減するための技術開発がもともと盛んな分野だ。ところが、大きなエアポケットがある。トラックなどの大型ディーゼル車向けの排ガス触媒である。
トラックメーカーは、乗用車メーカーほど規模が大きくないので、「自力で触媒開発を行うよりも、良い触媒があったら使うという考え。技術開発の主体は触媒メーカーだった」(産業技術総合研究所新燃料自動車技術研究センター副研究センター長の浜田英昭氏)。
触媒の開発はノウハウの積み重ねなので、触媒メーカーは技術の内容はほとんど外部に出さない。その閉じた世界に多様な分野の研究者が加われば、新しい可能性が開けるのではないか。こうした思いが出発点となって、浜田氏がリーダーとなった大型ディーゼル車の新規触媒開発プロジェクトが始まった。
大型ディーゼル車の排ガス浄化システムは、ガソリン車とは大きく異なるが、技術開発のステップは共通する部分が多い。すなわち、(1)触媒活性種の探索、(2)触媒活性種の複合、(3)担体構造の高度化、である。このプロジェクトには、この三つのステップがすべて含まれている。
〔以下、日経ものづくり2011年1月号に掲載〕
超硬工具(W)◆追求し切れていない2番手の潜在力引き出す
超硬合金は一般的に、タングステン(W)の炭化物である炭化タングステン(WC)と、コバルト(Co)などの粉末を混合して焼き固めた材料だ。この種の超硬合金を使った工具(超硬工具)にはWCが80質量%以上含まれることも多く、Wの主要な用途の1つとなっている。
ところが、Wの生産の約80%が中国に集中している上、価格上昇も続く。Wの価格は2005年に高騰し、その後にいったん緩やかに下降したが、2010年に再び上昇。同年12月には、2005年の最高値を更新した。
超硬工具は、高精度の加工を短時間で行える工具として重宝されているが、その材料の多くを超硬合金に依存する。そこには上述したWにかかわるリスクがあることから、超硬合金を代替できる工具用材料としてサーメットに期待が集まる。特に、炭化チタン(TiC)や炭窒化チタン〔Ti(C,N)〕を主成分とするサーメットである。
サーメットは既に工具用材料として使われている。ただし、強度や破壊靱性、熱伝導性の点で超硬合金に劣り、それに次ぐ「2番手」という位置付けだ。逆に言えば、現在の超硬合金が「粒子を微細化する焼結技術や添加剤の開発など、さまざまな試行錯誤の結果として生まれた」(産業技術総合研究所サステナブルマテリアル研究部門相制御材料研究グループ長の小林慶三氏)のに対し、サーメットの潜在力はまだ十分に引き出されていない。工具分野においてレアメタル依存症から脱却するには、サーメットの開発がカギを握る。
〔以下、日経ものづくり2011年1号に掲載〕
Part3:さらば使い捨て
後回しだったリサイクル 国内資源活用に本腰
レアメタルを自給できないなら、とことん再利用すればよい。既にレアメタルを使ったハイテク製品が日本国内にあふれ、都市鉱山と呼ばれている。寿命が尽きた製品から大量のレアメタルが取り出せるはずだ──。ところがそれが、一筋縄ではいかないのである。
日本は2000年前後から国を挙げてリサイクルに取り組んできた。ものづくりに関連が深い分野に限っても、家電リサイクル法(2001年4月施行)や自動車リサイクル法(2005年1月施行)、パソコンや複合機を対象にした資源有効利用促進法(2001年4月施行)など、次々とリサイクル関連法がスタートした。しかし、これらは循環型社会の構築、もっと具体的にいうとごみ削減が最大の目的だった。当時は、産業廃棄物の最終処分場が満杯になるまで、2年もないと推定されていて、ごみ削減が喫緊の課題だったのだ。
そのため、大量に廃棄される製品や簡単に処理できない製品といったゴミ削減効果の大きい製品がリサイクル法では優先された。実際の再資源化でも鉄や銅、アルミニウム(Al)合金、樹脂など量が多い汎用素材が中心だ。レアメタルのように絶対量が少なく、しかもさまざまな製品/部品に薄く分散して使われる素材は、リサイクルの輪の中からすっぽり抜け落ちたのである。つまり、「レアメタルは、現行のリサイクルシステムに馴染みにくい」(経済産業省リサイクル推進課総括補佐の吉川尚文氏)のだ。
このため、レアメタルをリサイクルの輪の中に入れるには、さまざまな技術開発や社会制度の整備が必要になる。レアメタルはリサイクルに関して完全に後手に回っている。根本的な解決法は新たなリサイクルシステムを構築することだが、それには時間が掛かる。だから、経産省は、やれるところをまずやる、というスタンスだ。これがレアメタルリサイクルの現状である。
〔以下、日経ものづくり2011年1月号に掲載〕