日本の強みである品質の高さや精度の高さといった高い付加価値。これを生かしつつ、コスト面での競争力を高めれば、日本のものづくりはまだまだ強く換なれる。ヒントは、従来のつくり方の常識を見直すことにある。(中山力、吉田勝)
不二製作所:ブラスト加工で磨く
砥粒が突き出た弾性体を噴き、表面を滑らせて凹凸を減らす
ブラスト加工といえば、砂や微小な鉄球などの硬い粒子をワークに吹き付けて表面のスケールやさびなどを取り除き、適当な表面粗さを得るためのもの──。だが、そんな常識はもう古い。さまざまなブラスト加工法を提案している不二製作所(本社東京)取締役開発部長の石橋正三氏は、「今は、あらゆる物質を噴射するエネルギ源としてブラスト加工をとらえている」と語る。このように見方を変えれば、さまざまな使い方が考えられる。
例えば、同社が開発した加工法の中でもひときわユニークな「シリウス加工」は、砂や鉄球でワークを「叩く」のではなく、研磨剤で「磨く」。この加工を金属部品の切削面などに施すと、鏡面のような綺麗な面が得られる。バフ研磨並みとまではいかないが、簡単な作業で顔が映り込む程度の面精度が確保できる(図1)。
「エアが通ればどこでも磨きやバリ取りができる」(同氏)のがシリウス加工の身上。実際、適用範囲は意外なほどに広い。溶接部表面のやけの除去、超硬工具の表面硬化など従来のブラスト加工の代替はもちろん、精密部品の微細なバリ取り、従来エッチングで除去していたレーザ加工のドロス除去、打ち抜き用のトムソン刃のエッジ加工など、既にさまざまな用途で利用されている。刃のエッジ処理は、従来の研磨では刃先が丸くなってしまうが、シリウス加工ならフィレットを整えて切れ味や耐久性を高める効果があるという。
〔以下、日経ものづくり2010年10月号に掲載〕
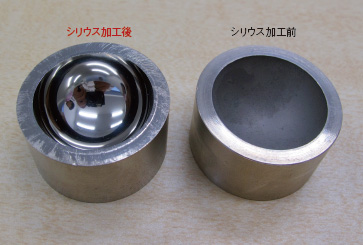
中田製作所:切削加工で磨く
搭載チップをあえて1つに、取り付け誤差の影響を排除
アルミ精密部品の切削加工を手がける中田製作所(本社大阪府八尾市)は、面粗さがRaで0.02μ~0.04μm(Ryで0.15μ~0.30μm)と高い品質の表面を通常の研磨ではなく、マシニングセンタによる切削加工で実現する(図2)。同社は、これを「鏡面切削加工」と呼ぶ。
研磨ではなく、切削加工で鏡面化したいというニーズは少なくない。例えば、研磨時の砥粒の破片がワークの表面に食い込んで残留することを嫌う真空装置の部品などだ。そのような部品に、熱反射/光反射といった性質を持たせたり、しゅう動性を高めたりといったニーズに対して同社の切削加工技術は対応できる。加えて、一般的なマシニングセンタで加工できるため、通常の切削加工と組み合わせて作業でき、そして何より加工時間が短い。ある程度の面粗さまで鏡面切削加工し、それ以上の面粗さが必要な場合には研磨と組み合わせるといった活用も効果的である。
〔以下、日経ものづくり2010年10号に掲載〕
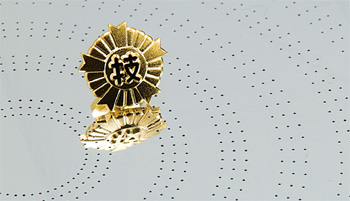
デルタ工業:低炭素鋼を使う
成形後に必要部分を焼き入れ、急速な加熱・冷却で強度を向上
「従来、焼き入れによって鋼材の引っ張り強さを高めるには、炭素やマンガンなどの含有量がある程度は必要だと考えられていた」(広島国際学院大学教授の李木経孝氏)。ところが、同氏とデルタ工業(本社広島県・府中町)が共同開発した熱処理技術を使えば、炭素含有量が極めて少ない鋼板の引っ張り強さを、数倍に高められる。
〔以下、日経ものづくり2010年10月号に掲載〕
三光合成:密度を変える
微細発泡で強度はそのまま、金型のスライドで中だけ軽く
薄くて軽く、かつ従来と遜色ない強度が得られる樹脂はないか。軽くて強い材料が求められる代表的な製品がクルマ。特に、今後増えると予想される電気自動車では重い電池が必要なだけに、他の部品には一層の軽量化が要求される。思い切って炭素繊維強化樹脂(CFRP)を使えば、鋼並みの強度で軽さは1/10にできるものの、非常に高価なため航空機のような特殊な用途でない限り、今のところ現実的な解とはなり得ない。
三光合成が開発した樹脂成形技術は、強度を損なうことなく軽量化したいという期待に応えるものだ。板物成形品の質量を3~4割削減できる。
〔以下、日経ものづくり2010年10号に掲載〕
世界最速試作センター:穴を積層する
めっき鋼板を順送プレス、打ち抜き部が細穴に成長
金属部品、特に大きさが数~数十mm程度の小さくて厚みのある金属部品に直径数百μmといった極細の長い穴を空けるのは極めて難しい。例えば、図3のような極細の穴の開いた部品を造ろうとしても、ドリルでは曲がりやすいし、放電加工でも深くなると削りくずを排出できない。しかも、一つひとつ機械加工するしかないため、コストが掛かる。メタル・インジェクション・モールドなら複雑な形状の部品も量産できるが、やはり製造コストが問題となる。いずれも家電製品などを量産する一般消費財向けの部品製造法としては実用的ではない。
これまで機械加工するしかなかった金属部品を安価に量産できないか──。その要望に応えるのが、世界最速試作センター(本社長野県岡谷市)が開発した、「積層間接合工法」と呼ぶ部品製造技術だ。薄い鋼板を重ね合わせて厚みのある金属部品を製造するもので、順送プレスで安価に量産できる。
〔以下、日経ものづくり2010年10月号に掲載〕
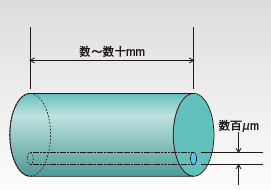
渡辺鋳造所:金型を鋳造する
氷点下に冷やして硬度アップ、鋳ぐるみで冷却管を最適配置
射出成形用の金型といえば、プリハードン鋼などのバルクの鋼材から削り出して造るのが一般的。それを鋳物で造れるようにするのが、渡辺鋳造所(本社山形市)が山形県工業試験センターと共同で開発したマルテンサイトの鋳鉄だ。
鋳物なら、金型を造る際にあらかじめ成形製品に合わせて造った冷却管のパイプを鋳ぐるんで造れることから、冷却管の設計自由度が大幅に高まる(図4)。
これまでも、冷却管を自由に配置するために粉末積層造形で金型を造る方法などが実用化されている。だが、柔らかい鋳物で金型を造るという発想はなかった。ところが、同社はもともと不良品だった硬い鋳物を別の視点から見直すことで、鋳造で造る金型を実現した。
〔以下、日経ものづくり2010年10月号に掲載〕
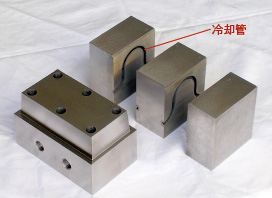
戸田精機:回転運動を駆使する
三角形の工具と2つのカムで、刃先の軌跡を四角形に
四角形などの角穴や内コーナーを加工する有力な方法として放電加工がある。それには当然、放電加工機や電極が必要になるし、実行すれば加工時間が長くなる。他の部分を切削加工している部品であるなら、わざわざ段取り替えせずに、角穴も切削加工したいと思うのが当然だろう。
しかし、切削加工のほとんどは工具をスピンドルで回転させてワークを加工する。つまり、工具の刃先の軌跡は円形となる。一般的な工具を使う以上、四角穴の角Rを工具の半径以下にすることは基本的に不可能だ。
〔以下、日経ものづくり2010年10月号に掲載〕
三木プーリ:均等にプレスする
金型の部分制御と質量管理で、粉末冶金を大物部品に適用
粉末冶金で造れる部品といえば、手のひらサイズの小型のものが多い。しかも「粉末冶金の焼結部品イコール、低密度でもろいというイメージがあった」〔三木プーリ(本社川崎市〕MLSTチームディレクターの大貫勝弘氏)ため、適用できる部品は限られていた。
しかし、同社が技術提携先である米Lovejoy社と共同開発した粉末冶金技術「MLST(Mikipulley Lovejoy Sintered Technology)」は、そんな思い込みに一石を投じる。一般の溶製材に引けを取らない高密度で、大型部品や複雑な形状の部品を造れるのだ。
MLSTは、NC装置を備えた多段成形可能なプレス機と焼結炉から成るシステムで、基本技術はLovejoy社が開発した(図5)。三木プーリは500tと1000tの2台のNC多段成形プレス機を導入しており、事業化に本腰を入れ始めた。「NC装置を備えた1000tの焼結用プレス機があるのは日本でもここだけだろう」(同リーダー小野裕氏)。
〔以下、日経ものづくり2010年10月号に掲載〕
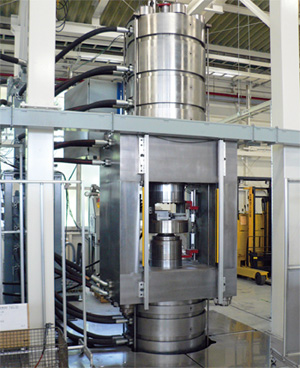
豊島製作所:加工硬化を制御する
金属の流れを見極めて工程設計、冷間鍛造の守備範囲を拡大
鍛造やプレス成形といった塑性加工は、切削加工などに比べて工数が少なくて済むため、ある程度の生産量があればコストダウンを期待できるつくり方だ。実現できる精度や形状の複雑さのレベルも向上しており、適用範囲は拡大している。
しかし課題もある。特に、常温で鍛造する冷間鍛造では、塑性変形に伴う加工硬化が最も厄介だ。複雑な形状の場合、最終形状までに焼きなまし(焼鈍)と表面処理(ボンデ処理)を何度も繰り返さなければならないこともある。これらの工数が増えるとコストアップ要因となり、「これで冷間鍛造の適用範囲の限界が決まったりする」〔豊島製作所(本社埼玉県東松山市)代表取締役社長の木本大作氏〕。
逆に言えば、焼鈍とボンデ処理を減らすことが、冷間鍛造の適用範囲の拡大へとつながる。それには、塑性流動を見極め、加工硬化を極力抑えることがポイントとなる。さらに、「冷間鍛造だけにこだわることなく、プレス加工やファイン・ブランキングなど他の塑性加工との組み合わせも考える」(同氏)。すると、今までは使えないと思っていた用途に冷間鍛造を適用し、低コスト化を図れる可能性がでてくる。
〔以下、日経ものづくり2010年10月号に掲載〕