「残業は増える一方なのに、給料は上がらない。できれば人を増やしてほしいけど、今の会社の状況じゃ、無理だろうなぁ」。そんなふうにあきらめモードになっている製造業関係者が少なくないのではないだろうか。リーマンショックから2年たち、戻り始めた受注量。でも、人の数は一向に戻らない。このままこの状況に耐え続けるしかないのか…。
いや、そんなことはない。本誌がここで提案をするのは、これまでの常識を覆す新しいカイゼンの実行である。名付けて「創造カイゼン」。カイゼンと言っても、製造現場だけの話ではない。設計現場でもきちんと効果を発揮してくれる。そんな創造カイゼンとは、何か。あきらめて残業に明け暮れる前に、その中身を知っていただきたい。(池松由香、高田憲一)
提言
ルーチンワーク増に現場は辟易
人を生かす「創造カイゼン」をせよ
未曾有の経済危機勃発から約2年。ものづくりの現場は今、「人手不足」という新たなる敵を前に呆然と立ち尽くしている(図1)。
2008年9月から2009年2月にかけて、日本の多くのメーカーは、売り上げが急落する危機に見舞われた。売り上げに対する固定費率が一気に増大し、大手メーカーが次々と数千人規模の人員削減に踏み切ったことは記憶に新しい。それから1年が経過した2009年秋ごろから、状況は徐々に変わり始めた。世界各国における在庫調整に一定のメドが付き、アジア諸国を中心に消費が戻り始めたことから、日本のメーカーの受注量も回復傾向に転じたのだ。
しかし、それに見合う増員策を決行するメーカーはほとんど見られなかった。「リーマンショックは、経済の不確実性を露呈した。受注が戻り始めたからといって、その先、どうなるかは分からない。そう考えるメーカーが増えたのではないか」。東京大学社会科学研究所教授の佐藤博樹氏は、メーカーが増員に踏み切れない理由をこう推察する。
〔以下、日経ものづくり2010年9月号に掲載〕
短編ドキュメント:三木ベルテック
“晴耕雨工”のカイゼン力で会社存亡の危機を乗り越えた
大きなガラス窓の向こうに、緑豊かな山々が見える。2010年8月、真っ盛りの夏を迎えた山形県米沢市にある三木ベルテックの会議室で、同社社長の安部功は社員たちの前に立ち、大きく息を吸った。
振り返れば、2008年9月のリーマンショックで、生産量は最大約1/3にまで落ち込んだ。それまで黒字だった月次決算も、2009年2月には大幅な赤字に転落した。それから1年半。こうして社員にうれしい報告ができる日が来るとは、あの時には想像すらできなかった。
「おととい、2010年7月の月次決算を締めました。営業利益率は12%。受注量も月を追うごとに増えています。無事、今期4カ月目を黒字で終えることができたのも、皆さんのたゆまぬカイゼン努力があったおかげです」
社員たちの顔を見回すと、皆、生き生きとした表情でこちらを見ていた。その傍らで、ムダとりコンサルタントでPEC産業教育センター所長の山田日登志が、満面の笑みを浮かべている。リーマンショック後、会社の危機を案じて毎月、指導に足を運んでくれたのだ。
〔以下、日経ものづくり2010年9月号に掲載〕
事例 製造1:リコーの「レイアウトフリー生産方式」
台車活用で人もラインも柔軟に
リコーのデジタル複写機の国内主力製造拠点である御殿場事業所(静岡県御殿場市)は、2008年のリーマンショック後も、人時生産性を半期で3~5%ずつ向上させることに成功している。その立役者となったのが、同事業所が独自に開発した生産方式。生産量や品種の変動に合わせて製造ラインの構成を自由に変更できる「レイアウトフリー生産方式」である。2003年から導入が始まり、現場の知恵と工夫でその後も進化を遂げている。この生産方式を確立したことが、同事業所の従業員が、より創造性の高い業務に当たるきっかけとなった。
〔以下、日経ものづくり2010年9号に掲載〕
事例 製造2:森精機の「オートキャンプ場組立方式」
配膳係居て、多能工輝く
中大型のマシニングセンタや旋盤加工機を製造している森精機製作所の伊賀事業所(三重県伊賀市)は、多能工をとことん生かす生産方式で受注増を乗り越えようとしている。リーマンショックで約1/3に激減した同社の受注は2009年秋ごろから反転し、2010年春にはリーマンショック前の約2/3にまで回復した。その一方で、受注減の打撃が尾を引き、2010年3月、同社では400人の依願退職者を募っての人員削減を余儀なくされた。以来、ほぼ同じ人数で受注増に対応している。
それを支える創造カイゼンが、「オートキャンプ場組立方式」だ。工場の床に四方形の線を描き、その区画(サイト)の中に、1台の工作機械を組み立てるのに必要な部品や工具をすべて用意しておく(図2)。一見、通常のセル生産と変わらないようだが、多能工の作業者が「本業」に集中できる工夫が詰まっているのだ。
〔以下、日経ものづくり2010年9月号に掲載〕
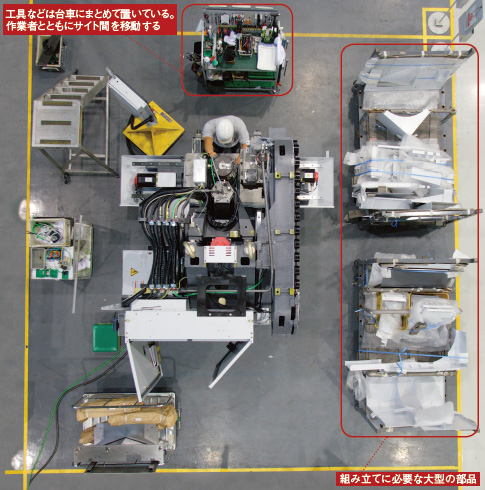
事例 製造3:菱和工業の無線通知システム
素材補充の効率化で多台持ち加速
「2009年前半の生産はピーク時の2割」と、金属部品の切削加工を主事業とする菱和工業(本社愛知県豊川市)の工場長の鈴木伸明氏は明かす。そんな状況では雇用を維持できず、21人の作業者を10人に減らさざるを得なかった。それでも、生産8割減に対して人員は半減にとどめたのである。
その後、同年後半から生産が戻り始めた。増員の代わりに、この回復局面で導入したのが、創造カイゼンだ。具体的には、素材の補充や段取り替えのタイミングを無線で通知するシステムである。菱和工業の生産は現在、ピーク時の7割前後まで戻ったが、10人で、基本的には残業なしで対応できているという。
〔以下、日経ものづくり2010年9月号に掲載〕
事例 設計1:富士通の「作業流れ図」
部門の狭間にボトルネックあり
設計/開発の分野で、象徴的な創造カイゼンがある。富士通のサーバ開発の事例で、熱解析用のモデル作成を半自動化したものだ(図3)。サーバの開発では、製品を適切に冷却してLSIに過度な熱負荷がかからないようにするため、使用時の温度を解析する必要がある。同社では、「基本検討」「詳細設計」「設計検証」「妥当性確認」の4段階で実施していたが、この創造カイゼンにより、サーバのプリント基板と実装構造の開発期間を一挙に24日短縮したのである。
〔以下、日経ものづくり2010年9月号に掲載〕
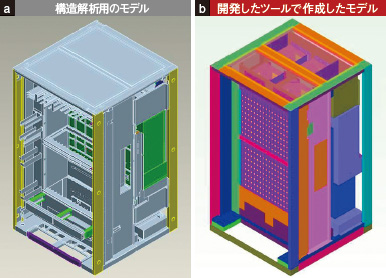
事例 設計2:リコーの設計業務支援システム
巨大なムダ生む“既知の無知”
設計現場でムダとりを実施しようとするとき、設計者の中からよくこんな意見が聞かれる。「設計者の仕事はムダが見えにくいから、カイゼンは無理だ」。確かに、目に見えるものを扱う製造現場に比べ、情報をやりとりする設計現場はムダが見えにくい。一見すると設計者がパソコンの前でボーッと画面を見ているだけのようでも、頭の中では着々と設計作業が進行している場合だってあるからだ。
しかし、だからといって設計者のムダとりは不可能ではない。ポイントは、製造現場のように「ムダを取る」のではなく、「ムダではない部分を残す」こと。カラー複合機の設計で設計者のムダとりを実施し、ある工程の作業時間を約1/10に削減することに成功したリコーの事例とともに、設計者のための創造カイゼンについて見ていこう。
〔以下、日経ものづくり2010年9月号に掲載〕
事例 設計3:埼玉富士の「VM活動」
多段進ちょく管理で手戻り撲滅
精密機器や自動車、電気電子製品などのさまざまな業種向けに小型部品の自動組み立て機を設計/製造している埼玉富士(埼玉県秩父市)FA事業部は、海外メーカーとの競争が激化する中、生産性を高めて利益を確保するために、中部産業連盟が展開している経営・管理手法「VM(VisualManagement)」を2006年5月に導入した(図4)。今では、設計部門で重点的に取り組んでいる。
同社代表取締役社長の堤繁氏は「リーマンショックの影響をもろに受けた2009年度は別にして、2006~2008年度はVM活動によって累計3億5000万円のコスト削減効果が得られた」と説明するも、「まだ十分ではない」という。設計部門などに大きなカイゼンの余地を残していると考えているからだ。
〔以下、日経ものづくり2010年9月号に掲載〕
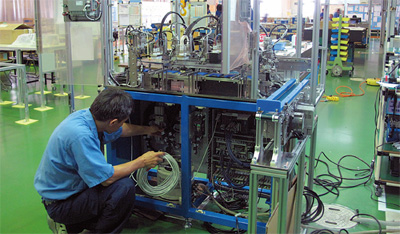