「IT導入で効率が上がるはずだったのに、現場はかえって多忙になってしまった」「IT導入で競争力が向上するはずなのに、今ではノウハウが失われ、アイデアがさっぱり出なくなってしまった」---。こんな症状に、心当たりはないだろうか。いずれも、ITの利用経験を積むにしたがって生じるものだ。単にITがうまく動いていないというだけでは、これらの症状が出ることはない。その症状が現れるには、原因がある。本来やってはいけないことをやっていたり、落とし穴にはまったりしていることがある。ただし、多くのケースでは、誰が見ても明らかな間違いだと、はっきり分かるようなものではない。ちょっとした考え方の差が大きな結果の違いを招いている。そんな、どちらにでも転ぶような要素がものづくりのITには多い。逆に言えば、ITへの取り組みは常に裏目に出る危険性をはらんでいる。そこを考慮して初めてITのメリットを享受できる。(木崎健太郎、富岡恒憲)
File1:慢性疲労1
設計ばかりに負荷を集中させる
ITツールを用いて設計検討を前倒しで実施するフロントローディングは、短い期間で良い製品を開発する上で王道ともいえる方法だ。しかし、その検討を実施するのは誰かといえば大抵、設計者自身。生産技術部門や購買部門の担当者が検討を始める前に、独自に製造性やコストなどの情報を収集し、検討を始めるというスタイルになる。 これは、生産技術や購買の担当者が担っていた仕事の1つが設計者に移る、つまり設計者の仕事が増えることを意味する(図1)。一つひとつの検討に時間をかけられず、甘くなって手戻りを誘発しかねない。
〔以下、日経ものづくり2010年7月号に掲載〕
File2:慢性疲労2
3次元データがあるのに情報伝達は2次元
「設計の成果を3次元データとして残しているのに、なぜ(従来通りの)2次元図面も作らなければいけないのか」。これは、3次元CADを活用している設計現場から聞こえてくる代表的な不満の1つだ。設計を3次元化したら2次元図面はなくなるはずだったのに、現実は違った。
設計現場で2次元図面を作るのは、後工程からの要望によるところが大きい。3次元データには2次元図面をはるかに超える情報が盛り込まれている。にもかかわらず、後工程での使い勝手は2次元図面よりも劣る。そこで、「2次元図面が欲しい」とせがまれるのだ。
〔以下、日経ものづくり2010年7月号に掲載〕
File3:慢性疲労3
標準化を伴わないCAD活用
「2次元CADで設計していたころよりも、設計時間が延びてしまった」。設計を効率化するために導入したはずの3次元CAD。だが、その使い方を誤ると、こうした落とし穴にはまってしまう。
実際、金型メーカーのモルテック(本社川崎市)では、3次元CADによる金型のモールドベースの設計を開始した当初、「2次元CADで設計していたころの2倍近い時間がかかった」(同社代表取締役の松井宏一氏)と明かす。誤解がないように付け加えておくと、3次元CADの操作の習熟度の問題ではない。
3次元化で設計時間が延びる最大の要因は、幾何学的に矛盾のない立体形状を作成しなければならない点にある。2次元図面では省略したりあいまいなまま進めたりしていた部分を、しっかりと形状定義しなければならないからだ。加えて、(1)押し出したり回転させたりと、平面的な図形(スケッチ)を立体化する必要がある、(2)単なる作図のツールだった2次元CADと違って、3次元CADは機能が豊富で必要な機能を選択するまでの操作回数が多い。これらの点も、設計時間を延ばす方向に作用している。
〔以下、日経ものづくり2010年7月号に掲載〕
File4:ノウハウ欠乏症1
効率向上で空いた時間をムダ遣い
3次元CADやPDMなどの設計開発システムの導入時に期間短縮を目指すことは「常識」であり、実際に目標を達成した企業は多い。にもかかわらず、それで本当によかったのかという反省が生まれ始めている。
かつて、セイコーエプソンで設計3次元化などを主導した坂井佐千穂氏(現・住商情報システム製造ソリューション事業部PLMソリューション・ものづくりITアドバイザー)は「日本企業は大きく効率を上げてきたはずなのに、リーマンショックで業績を大きく悪化させた」と指摘する。海外と比べて景気回復のテンポも遅い中で、「どう頑張るかといえば、さらに効率を上げるしかなくなってしまっている。効率を上げることは重要だが、それだけでは疲弊するばかりだ」。
〔以下、日経ものづくり2010年7月号に掲載〕
File5:ノウハウ欠乏症2
非正規雇用者がIT操作超えてコア業務も
リーマンショック前の好景気のころ、多くの企業で技術者が不足し、設計開発の現場でも派遣など非正規雇用の形で活躍する技術者が増えた。3次元CADの運用に関しても、本誌調査によれば約半数の企業が「正社員も非正規雇用者も、区別なく3次元CADを使っている」と回答している。つまり、非正規雇用者は社員の指示に基づいてモデリングだけをこなしているわけではなく、実質的な設計作業を担当している実態がある。
むしろ社員は管理業務に回り、本質的な設計業務は専ら非正規雇用者、という設計現場が珍しくなくなっていた。その結果、社員にノウハウが蓄積できず、非正規雇用者の雇い止めや退職とともにノウハウが失われる、という問題が起こっている。
〔以下、日経ものづくり2010年7月号に掲載〕
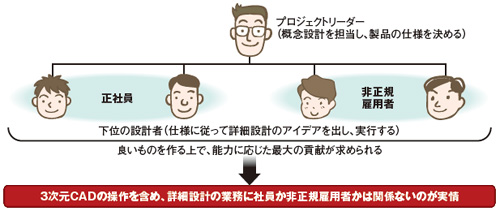
File6:情物分離症1
設計データが現物と一致していない
製品開発も終盤。不具合に気付き、後工程の現場で金型に手を入れる。しかし、忙しいこともあって、修正した点を上流のデータへフィードバックするのをついつい後回しにしてしまう。場合によっては、そのままフィードバックを忘れてしまうことも。その結果、修正点が反映されていないデータを次の製品の開発過程で流用し、同じ過ちを繰り返すことが間々ある(図3)。
理想を言えば、変更したら即座に関連する全データにそれを反映すべき。しかし、製品開発にかかわるデータは、設計データ、生産用の製品データ、金型データ、加工用データ、検査用データ、組立データなど多種多様。これらすべてを変更のたびに修正していては、その工数だけでもたまらない。
現実問題として、これらのデータはどこまで現物と一致させるべきなのか──。ものづくりIT活用に詳しい専門家に聞いたところ、おおむね「流用する可能性のあるデータは、最終的なものに更新しておくべき」という意見だった。
〔以下、日経ものづくり2010年7月号に掲載〕
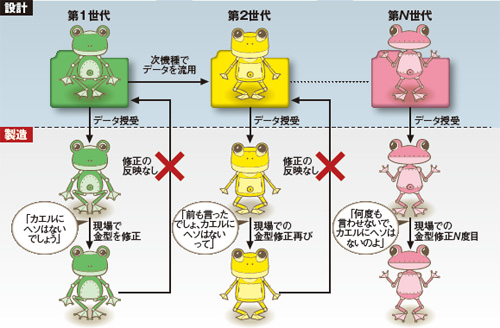
File7:情物分離症2
部品表が現物と一致していない
自動車/家電メーカーといった見込み生産中心の大企業と、産業機械/設備機械のメーカーや受注生産中心の中小企業では、求められるITシステムの内容がかなり異なる。これまでは、単純に自動車や家電のメーカーはIT化が進んでいて、産機や設備のメーカー、中小企業が順次その後追いをするといった見方が多かった。システムの内容も、大企業向けのものをスケールダウンしてコストを抑えたものでよい、という考えが主流だった。
しかし、実際にはそう単純な構造ではない。自動車/家電のメーカーが大量生産で消費者向けの大きな市場をカバーする一方で、産機/設備メーカーや中小企業は専門的な技術で、それぞれ顧客の要望にきめ細かく取り組む。大量生産品はメーカーの手を離れたら普通はそれで縁が切れるが、産機や設備は顧客の元で長く稼働し、メーカーは顧客と長く付き合う。アフターサービスの在り方も異なる。
〔以下、日経ものづくり2010年7月号に掲載〕
File8:IT貧乏症1
アプリやデータの管理は二の次
ITシステムを活用することには熱心でも、その管理方法には気配りが足らない。そうしたケースは珍しくない。アプリケーション・ソフトウエア(以下、アプリ)はローカルのパソコンにインストールされ、データも必要に応じてやりとりはするが、基本的にはローカルに個別管理。担当者以外のほとんどの関係者はデータの所在を知らない。
これでは、ITシステムを上手に使いこなしても、ライバル企業の上をいくコスト・パフォーマンス(C/P)をITシステムから引き出すことは難しい。アプリやデータのバラバラな管理による、工数やコストのムダが発生しているからだ。
それでも、クライアントサーバが全盛の一昔前なら管理方法を軽視しても、まだ差はつきにくかった。アプリやデータを集中管理したくても、回線負荷の集中という問題があって、当時の技術レベルではハードルが高かったからだ。
〔以下、日経ものづくり2010年7月号に掲載〕
File9:IT貧乏症2
目的なく電子データを長期保存
コンピュータ・システムの普及が進み始めた時期から、情報を長期にわたってどう保管・保存すべきかが重要な問題として議論されるようになった。コンピュータ技術の発展は急激で変化が大きく、アプリケーション・ソフトウエアもバージョンアップを繰り返したり、後継ツールが出現したにもかかわらずデータ互換性が完全ではなかったりする。電子データを長期間、いざというとき使えるように維持していく方法の案出は、難題とされてきた。
現在でも、データの長期保管・保存の手段として決定的なものはない。常にデータを使えるように、最新版ツールに合わせて変換し続けるには、工数とコストがかかる。変換しないで使えるようにしておこうと思えば、以前のシステムをハードウエアごとそのまま残しておけばよい。しかし、古いシステムは保守サービスがなく、故障したらそれっきりになってしまう。
記録として残すなら、紙に印刷するのが一番確実かもしれないが、物理的にかさばるし、火事などの災害に弱い。精密機器メーカーなどでの勤務経験がある技術者は、「デジタルデータにさえしておけば、(100%の精度ではないにせよ)変換処理をすればさまざまなところへ持っていけるが、紙ではそうはいかない」と言う。「ある部品メーカーは、これまでの設計資産をすべて紙で保有し、それを小学校の教室くらいの部屋に保管している。この部屋が火事になったら、設計資産は無に帰してしまうのが実情」(同技術者)だ(図4)。
〔以下、日経ものづくり2010年7月号に掲載〕
File10:IT貧乏症3
ITシステムのことは他人任せ
「IT部門の担当者は、もっと現場の業務について勉強すべきだ」。そう不満を漏らす、ものづくりITのユーザー部門の技術者は少なくない。現場のことを知らなければ、そこで使う優れたシステムを企画することは難しい。その意味で、こうした不満が出てくるのは仕方がないのだ。実際、ITの専門家からも「IT部門にとっての顧客は現場。営業マンが顧客のことを勉強するように、IT部門も現場のことを勉強するのは当然」〔デジタルプロセス(本社神奈川県厚木市)取締役相談役の間瀬俊明氏〕という声がある。だが、1つ疑問がある。果たして、ユーザー部門の担当者は、IT部門への不満を口にしているだけで優れたシステムを手にできるのだろうか。
〔以下、日経ものづくり2010年7月号に掲載〕