トヨタ自動車は2009年5月14日,2008年度の車両のリサイクル実効率が約97%に達したと発表した。既存の解体事業者などによる部品や金属材料の回収と,自動車メーカーが主体になって実施するシュレッダダストのサーマル・リサイクル(熱回収)や材料リサイクルを組み合わせて実現したものだ。
一方,キヤノンやリコーなどの複写機メーカーは,材料リサイクルよりもさらに環境負荷の低減効果も大きく付加価値も高い,部品の再利用を重視している。キヤノンは2005年8月の段階で,約9割の部品に再利用品を使った複合機を商品化。リコーも,再利用部品を多く組み込んだ再生複合機事業の黒字化を2006年度に達成している。
このように,リサイクルを効果的に実行している業界でも,具体的なリサイクルの内容はそれぞれ異なる。従って,リサイクルのための設計方針も変わる。熱回収と部品の再利用では対応するための設計が全く違う。熱回収する部品は解体/分離する必要はないが,再利用する部品は簡単に解体/分離できなければならない。
「全部やる」のは非現実的
「設計時にリサイクルに役立つことを全部やるのは,一見,正しい考え方のようだが,負担が増えて設計者が疲弊するし,必ずしも効果が上がるわけでもない」と, 家電メーカーの元設計者で,リサイクル設計に関する著作もある東京造形大学准教授の山際康之氏は指摘する。リサイクル率を100%に近づけることは技術的には難しいことではないが,掛かる費用と手間から見て現実的ではない。設計実務では,どんなリサイクルを想定し,何を優先させるかを判断することが重要なのである。
特に日本のリサイクル政策は,製品ごとに,個別のリサイクル法が乱立し,それに応じてリサイクルの仕組みも異なるのが現実だ(図)。
〔以下,日経ものづくり2009年6月号に掲載〕
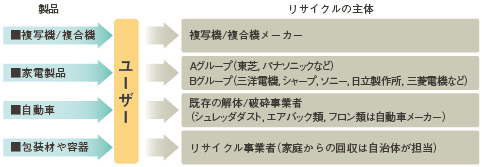