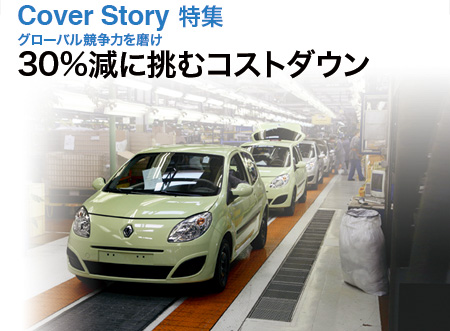
環境・安全規制の強化、原材料の値上げで自動車のコストはますます上がる。その一方で、中
国やインドなど新興市場での競争が激化し、低価格車のニーズが増している。コストアップの逆風を
跳ね返し、グローバルな価格競争力を高めるには設計・製造の大胆な改革が必要だ。部品の一体化、
新構造の採用、材料・工法の転換によって30%減を目指すコストダウン手法を探った。(林 達彦) |
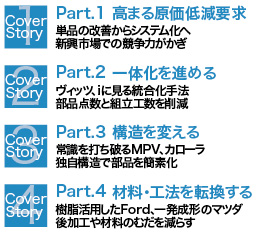
自動車メーカーの原価低減額は年々薄れ、いまや多くても売上高比で1 %程度。
しかも苦労して生み出した成果も原材料費の値上げで帳消しになってしまう。
新興市場での競争力強化も課題となっており、一層のコストダウンが求められる。
購買戦略や共用化の努力は続けられているが、コストの80 %は設計段階で決まる。
設計・製造を大幅に見直しせば30 %減を目指したコストダウンは可能だ。
2007年5月、東京でトヨタ自動車の決算説明会が開かれた。販売台数増によって売上高、営業利益、純利益ともに過去最高を更新したことを発表した渡辺捷昭社長は、今期に取り組むテーマの一つとして、新たに進めているコストダウン活動「VI(Value Innovation)活動」について触れた。
トヨタは2000年から世界で最も高い品質、価格競争力を目指した「CCC(Construction of Cost Competitiveness)21」活動を実施してきた。購買金額の90 %を占める主要な170品目について、平均30 %の削減を狙った活動である。この成果として同社は4年間で約1兆円のコスト低減を実現した。
VI活動は、部品単品ではなく複数部品の機能を統合して、コストダウンや新機能を実現しようとするもので、CCC21を上回るスピード、規模、低減効果額を目指している。
発表会の席上では、電子化に伴って増え続けるECU(電子制御ユニット)を例にとり、機能を「ボディ」「シャシー」「パワートレーン」などに分類し、点数の削減や小型化、新たな機能を盛り込むことを表明した。渡辺社長は「2008年には成果を取り入れたクルマが登場する」と述べた(図)。
コストダウンの本家ともいえるトヨタが、新たな活動を立ち上げたのは、材料の高騰や環境・安全規制の強化によるコスト上昇に対応するため、これまで以上に新しい手法が求められていることがある。
図●トヨタ自動車はVI活動を推進
VI活動ではシステム単位の原価低減活動を推進する。ECUの例では機能を分類して複数のECUを統合することを狙う。
コストダウン手法として多くのメーカーが取り組むのが従来複数あった部品を一体化する手法だ。
市光工業はトヨタ自動車のCCC21活動の成果としてドアミラーのハウジングを一体化、
ジェイテクトはその先のVI活動を見据えたハブユニットを開発中だ。
モジュール化を進めたのが、三菱自動車とカルソニックカンセイ。「i」のクーリングモジュールは、
コストを20 %下げ、カルソニックカンセイもコンデンサ一体型ラジエータを実用化。
市光工業:軽量ドアミラー |
2005年に全面改良したトヨタの「ヴィッツ」、そして2006年に全面改良した「カローラ」はトヨタのCCC21活動の成果を盛り込んだ戦略車種だ。この両車に搭載されているのが、市光工業が開発した軽量ドアミラーである。従来のミラーはハウジングが2部品に分かれていたが、これを一体成形することでハウジングを約40 %軽量化した。コストダウンについてもCCC21の目標に合わせ30 %を目指して開発を進めた。 |
|
機能の一体化をさらに進めた設計の最適化手法が新しい構造の採用だ。
従来の常識にとらわれない構造の見直しは、電気部品のジャンクションボックスにも及ぶ。
日本ブレーキ工業の駐車ブレーキやポーライトの焼結部品はMPVのコスト削減に貢献。
アイシン高丘もカローラで排気マニホールドを一新した。
Bosch社は製造しやすい構造によって、ABSモジュレータを30 %コストダウンした。
三菱電線工業:ジャンクションボックス |
部品コストの8割は設計時点で決まるといわれる。Part2で紹介した機能の一体化と並んでコスト低減に有効なのが構造を大胆に見直すこと。ここでは、従来の常識を捨てて新構造を採用した例を紹介していく。 |
|
材料や工法の転換によって構造を大きく変えずにコストダウンすることも可能だ。
ここでは樹脂やアルミ合金で軽量・低コスト化した例、工法転換で工程を減らした例をみていく。
樹脂化で効果を上げたのは、AT用のプラグでの白山製作所、クラッチレリーズ軸受での日本精工など。
工法転換ではAT用のクラッチハブを一発成形したマツダ、マフラーをレーザ溶接で
40 %コストダウンした三五などを取り上げる。
白山製作所:AT用バルブボディのプラグ |
AT(自動変速機)の油圧回路を切り替えるバルブボディには、スプールバルブやバルブ、スリーブ、プラグといったさまざまな部品があり、材質としては鋼もしくはアルミ合金が使われている。 |
|