早いもので、本連載も最終回である。今回は、「これからの日本のものづくり」と大上段に構えて、生産現場だけではなくものづくりのプロセス全体に視野を広げつつ、過去9回のコラムをまとめよう。
1人完結へのこだわり
デジタルセル生産でのこだわりは「1人完結」だ。筆者は、ものづくりの理想の姿は製品の開発から設計、生産、販売、そしてサービスに至るまで、全てのプロセスを1人で完結することだと信じている。産業革命以前の家具職人のイメージである。
とはいえ、現代において、それを完全に実現するのは難しいことも承知している。そこで、より現実に即して理想に向かってできるだけ多くのプロセスを1人で完結させたい*1。
その根拠の1つが、工程内をスイスイと動き回ることから「ミズスマシ」と呼ばれる部品供給要員の配置である。筆者は、このミズスマシに対して否定派だ。例えば100人の組立作業者に対し、5人のミズスマシを配置したとしよう。もし10人から同時に部品供給の依頼が来たらどうなるか。少なくとも5人の作業者は当然しばらく待たされる。いわゆる「手待ちのムダ」の発生だ。逆に、誰からも呼び出しのない時間帯が10分間続いたら、ミズスマシの方が何もせずに待機することになる。やはり、ミズスマシを使って分業することでムダが発生する。
さらに根本的な疑問もある。一日中、部品の供給を繰り返すミズスマシの仕事を「楽しい」と感じる人はそれほど多くはないのではないか、ということだ。
ミズスマシなど使わずに、作業者は自分のセルに部品供給が必要だと判断したら、自ら部品庫に必要な部品を取りに行けばよい。「それは歩行のムダだ」と思われるかもしれないが、その際の歩行距離はミズスマシと変わらない。何より、筆者の経験および作業者からのヒアリングによると、組立作業における肉体疲労度は「立ちっぱなしの作業」が最も高く、次いで「座りっぱなしの作業」だ。実は、1人完結セル生産における「立ったり座ったりし、時には歩く」という作業形態が最も疲労度が低いのである。「常識」が常に正しいとは限らない。
分断するとムダになる
分業化のデメリットを示す事例をもう1つ紹介しよう。セル生産を構築するに当たって、どうしてもやりたくなってしまうのが、ユニットを組み立てる「サブアセンブリ組立セル」を設置することだ。多くの製品に使われるユニットはまとめて造った方が生産効率は高いのだから、そのユニットに対しても組み立てには専用セル(サブアセンブリ組立セル)を使おう、という考えだ。
筆者は、この考え方も否定する。まず、サブアセンブリ組立セルとメイン組立セルとの同期を取らなければ、欠品による手待ちのムダ、あるいはその逆に、行きすぎてしまう仕掛りのムダが発生する。その対策としてPOP(生産時点情報管理)を使って同期システムを組めばいいと考える人もいるだろう。だが、そんな余計なシステムを作って運用することこそがムダなのだ。
サブアセンブリ組立セルには根本的な大きな問題点が存在する。そこに割り振られた作業者が、「私はメインの組み立てがあまりうまくないからサブアセンブリに回されたんだ」と感じてしまうことだ。1人完結セル生産の導入によってせっかく醸成された作業者の前向きなマインドが崩れ、「明るく楽しい現場」が一転、「暗くつらい現場」に後戻りしてしまう。
1人完結セル生産を一度構築したら、それを分割するたびにムダが生じる。分割することを考えてはダメ、逆なのだ。いかに1人完結の範囲を広げるかを考え続けるべきなのである(図1)。
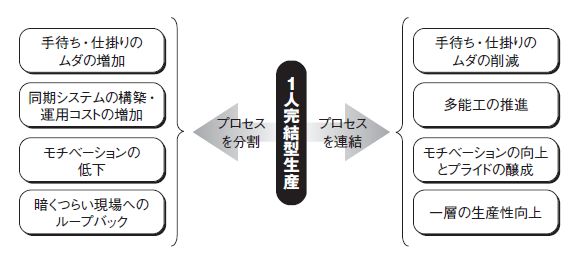