デジタルセルから得られるデータを分析すると興味深いさまざまな真実が見えてくる。図3はある機種を担当するAさんとBさんの2人の作業者を対象に、1台ごとの組立総工数(分)をグラフ化したものだ。
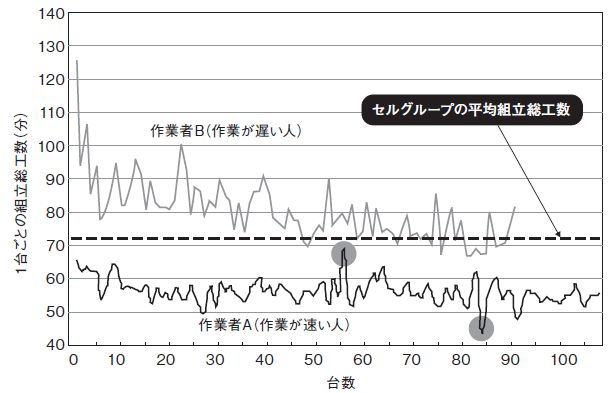
Aさんは作業が速いと定評がある。この製品群(セルグループ)全体の平均組立総工数を超えることはない。一方、Bさんはあまり作業が速くない上に、この機種を担当するのは数カ月ぶりだ。よって1台目は平均組立総工数の2倍近くかかってしまったが、徐々に勘を取り戻し、30台目あたりからは自身の実力付近の値まで回復するが、平均組立総工数を下回ることは数えるほどだ。
多くの生産管理スタッフはこの2人の実力差を問題視することだろう。だが、筆者はこれで全く問題ないと考えている。AさんとBさんを含むセルグループ全員で生産台数をこなせばよいと考えるからだ。
仮にライン生産において、AさんとBさんを含む10人でラインを構成したとしよう。各作業者が担当する工数はセル生産の1/10になるため、各作業者の組立総工数は絶対値としてはこんなに差は出ない。しかし、平均組立総工数を基準にして工程設計を行うと、作業の遅いBさんは常にラインに追われるどころかタクトタイム内に作業を終えることがなかなかできない。この影響はBさんの次工程の作業者にも及ぶ。タクトチャイムが鳴っても製品が流れてこないため作業できなくなるのだ。これを防止するために生産管理スタッフは各作業者の間にバッファ(仕掛品)を置くことになる*3。