電気自動車に搭載する部品は,既存のガソリンエンジン車などとは大きく異なる。当然,その設計や生産のスタイルも違ってくるはずだ。現在のところ,継続的に電気自動車を量産しているのは世界でも三菱自動車の「i-MiEV」だけ。その生産現場をまず,見よう。
i-MiEVを生産しているのは,同社水島製作所(岡山県倉敷市)の軽・商用車工場である。水島製作所の建物の延べ面積が52万m2であるのに対し, 軽・商用車工場は1万125m2。とてもコンパクトな工場だ。そこに設置された全長207mの組立ラインで,輸出仕様の「デリカ」や「パジェロミニ」と共 に混流生産されている(図1)。ラインで作業する従業員数は90人ほどである。
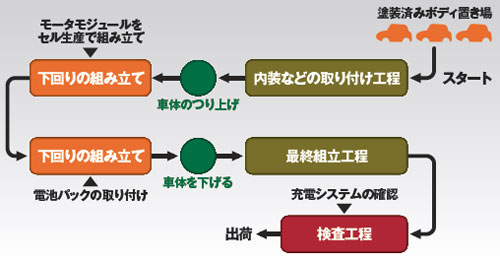
モータモジュールをセル生産
同製作所は,ベースとなったガソリンエンジン車の「i」も生産しているが,iは別の建屋の高速量産ラインが担当する。軽・商用車工場には塗装済みの車体が供給され,モータやリチウム(Li)イオン2次電池などを組み込み,i-MiEVが出来上がっていく。
まず目に付くのは,モータモジュールの組み立て/取り付け工程だ。メインの組立ラインの脇に昇降台車を兼ねた作業台があり,その周りにモータ,インバー タ,DC-DCコンバータ,リアサスペンションなど10数個の部品が用意してある。こうした部品を,一人の作業者がセル生産方式で組み立てる(図2)。専用の組立工場があるガソリンエンジン・モジュールとは大違いだ。
リアサスペンションやモータなどの重い部品は,ホイスト式の小型天井クレーンを利用して作業台まで持っていく。生産が始まって間もないはずなのに,作業 者は慣れた手つきで電気自動車の心臓部を組み立てていく。約25分で完成。別の担当者が5分ほどかけて品質確認作業を行った後,車体への取り付け工程に入る。
作業台はメインの組立ラインに向かって自動的に動いていき,流れてくるi-MiEVの車体後部の真下で止まる(図3)。作業台は,そのまま昇降機の役割 を果たしてモータモジュールを持ち上げ,その状態で車体への取り付け作業を行う。i-MiEVは現在,1時間当たり1.5台のペースで生産している。モー タモジュールの組み立てに約30分かかるので,生産量が増えて1時間当たり2台を超えると間に合わなくなる。その場合は,作業台を二つにして対応する予定 だ。
この方式は,混流するガソリンエンジン車の生産を乱さない上,生産性も高いという。そのカギは,モータ・マウント・フレームを車体から独立させたこと だ。i-MiEVの車体は,可能な限りベースのガソリン車と共通化してある。そこにガソリン車にはない部品を素早く取り付けるには工夫が必要になる。
一般的には,モータ・マウント・フレームを車体(ホワイトボディ)に一体化した方がコストを抑えられる。ところがこの方法だと,「モータとリアサスペン ションは下から,DC-DCコンバータとインバータは上から取り付けることになる。すると,メイン組立ラインでの工数が増えて,ガソリン車の流れと合わな くなってしまう」(同社生産技術本部組立生産技術部)。これを避けるため,モータ・マウント・フレームをモータモジュール側に取り付けて下から一気に車体 に組み込めるようにしたのだ。
メイン組立ラインの脇でセル生産といった柔軟な対応ができるのは,軽・商用車工場のメンバーはチームワークが良く,技能に優れた人材がそろっているから だ。こうした強みは,工数が多いクルマを少量生産する中で培われた。「普通の組立ラインでの1工程の作業時間は1分程度だが,軽・商用車工場では3分程 度。複雑な作業にも対応できる」と,三菱自動車水島製作所軽・商用車組立工作部長の須江隆行氏は胸を張る。当初はベース車のiと混流生産する案もあった が,機動性と柔軟性が見込まれて,軽・商用車工場が担当することになったという。