「公差設計を勉強し直したいという企業が,2年くらい前から急激に増えている」。こう語るのは,公差設計のコンサルタントなどを行っているプラーナー(本社長野県・下諏訪町)で代表取締役を務める栗山弘氏だ。「相談してくるのは,最初は電機メーカーが中心だった。しかし,今は自動車業界からの依頼も増えている。企業規模も中小から大手まで幅広い」(同氏)。
公差は,ものづくりに携わる技術者にとって基本中の基本。設計で決めた部品の形状や大きさが,実際に製造したときにその通りになるとは限らない。必ず発生するバラつきを,どの程度許容するのか─。公差情報は,設計内容を実体化する上で不可欠な,設計と生産の懸け橋である。
しかし,その公差をいま一度,学び直そうというメーカーが増えている…。一体,日本のものづくりの裏側で何が起こっているのだろうか。
公差が危ない
日本のものづくりを支えているのは,高品質かつ低コストという強い競争力だ。その土台が,長年培ってきた公差のノウハウである。しかし今,この土台が崩壊の危機に直面している【図1】。
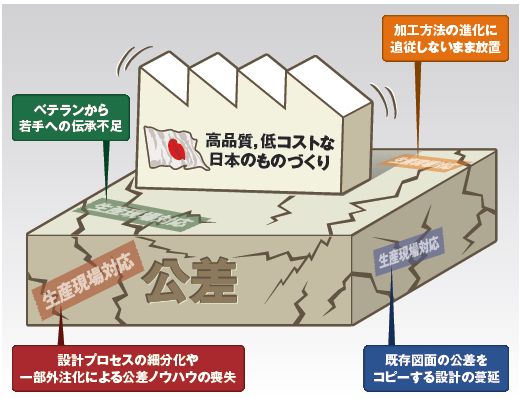
公差に対する取り組みが軽視されてきた結果,不適切な公差のはんらんが進んだ。この状況を打破しなければ,近い将来,日本のものづくりの競争力は失墜する。
その結果,設計現場で何が起こったか。公差の検討時間を節約するため,設計者の多くが,既存製品の公差の流用に走ったのだ。短期間で限定的なら,流用は効率的な設計法だ。しかし,安易な流用が長く続くと,なぜその公差にしたのかという知識やノウハウが次第に失われ,その伝承も断絶してしまう。特に,若手技術者が公差に関する実践的な知識を習得する機会がなくなり,机上の空論に陥る【図2】。
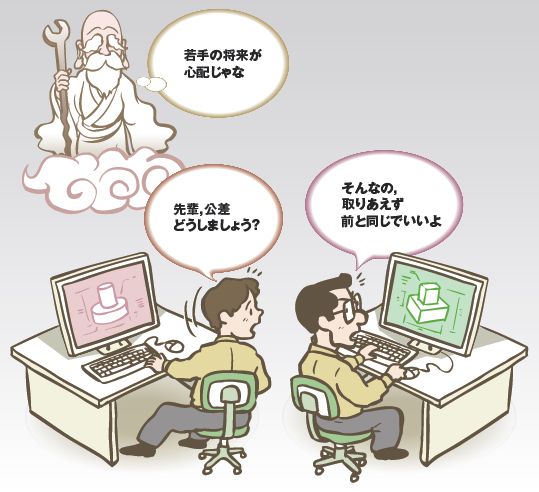
そもそも,機械系の大学教育における公差の位置付けも低くなっている。「幾何公差なんてとんでもない。はめ合いを教える程度にとどまる」(海上技術安全研究所環境エンジン開発プロジェクトチーム/機関システム開発研究グループグループ長の平田宏一氏)。
第二に,加工現場の変化である。新しい工法が登場し,数値制御技術や工具など,工作機械に関する技術も年々進化している。結果,実現できる精度とその容易性も刻々と変化している。
本来,公差は加工方法と密接に関係して決まるもの。そのためには,設計と生産の密接な情報の交換/共有が不可欠である。ところが,この公差に関する情報の交換/共有がうまくいかなくなってきているというのだ。
「昔は,図面を見ながら加工精度を相談し,図面に注記として書き込んでいた。ところが今は,CADデータだけを送ってきて,一言の説明を受けることもなく加工しなくてはならない」(ある加工メーカーの技術者)。これは外注先だからということではなく,社内に加工現場があっても足を向けたことがない設計者が増えているという。
設計のフロントローディングを進めるコンカレント・エンジニアリングの導入によって,設計の初期段階から生産部門の技術者が参加するデザインレビュー(DR)を開催する企業は増えている。そこで公差についても検討されていれば,前述のような問題は起こらないのだが,DRの早い段階では具体的な公差値が決まっていなかったり,加工や組み立て,メンテナンスといった作業の可能/不可能といった判断しかできなかったりという状況で,一般に公差の検討は対象にならないようだ。