成型,印刷,接合によってフィルム基板に機能素子を集積,個片化してデバイスを作る。このような新たな製造技術「システム・オン・フィルム」が,電子デバイスの量産技術の候補として浮上してきた。製造したデバイスは,フィルム基板をベースとしているため,薄く,軽く,曲げられる。フラットパネル・ディスプレイ(FPD),太陽電池,無線タグ,LSI,MEMSデバイス,電源デバイスなど幅広い分野で利用できるようになる(図1)注1)。
注1)究極の姿として,ディスプレイ,ロジックLSI,メモリー,無線通信機能,電源まで1枚のフィルムに集積する。
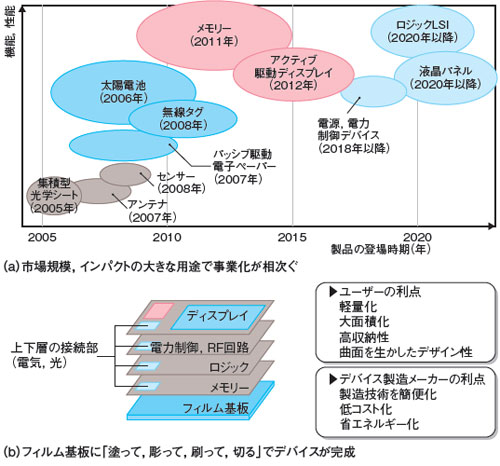
システム・オン・フィルムが従来と異なるのは,基板がSiやガラスといった硬い無機材料から,薄く柔らかい有機材料に変わることだけではない。製造技術上で二つの大きな特徴がある。一つは,フォト・リソグラフィを使わず,印刷と成型を利用する点にある。製造装置がケタ違いに安くなり,材料使用効率が大幅に高まる。もう一つは,ロール状に巻いた長さ数百m~数kmのフィルムを使って連続的に生産するロール・ツー・ロール方式の採用である。多くの製造装置を連結して搬送用装置や手間を省略できる。この二つを組み合わせることによって,デバイスの製造コストをケタ違いに下げられる。
このような製造手法のコンセプトは以前からあったが,これまで光学フィルムやフレキシブル基板の製造に限られていた。ここへ来て加工技術の精度や材料の信頼性が向上し,能動的な機能を備えた電子デバイスの量産にも適用できるようになった。
非真空下で効率的に製造,コストを大幅低減
ここでいうシステム・オン・フィルムとは,フィルム基板に電子デバイスやシステムを形成する製造技術である。製造コストを大幅に下げられる点が最大の特徴である。工程によっては,製造装置の初期コストが最大で2~3ケタ低くなり,材料コストは半分以下に下がる。
製造コストを低減できるのは,高価な製造装置を使わないことによる。既存の半導体やディスプレイの製造には,真空チャンバを備えた数千万~数十億円という製造装置を利用している。これに対してシステム・オン・フィルム技術では, 1000万円程度の印刷機や成型機,樹脂の塗布装置,レーザー加工装置,ラミネート装置などを主に使う(図2)。しかも材料の利用効率が高い。リソグラフィをベースとする既存の半導体やディスプレイの製造プロセスでは,基板全面に材料を載せてから不要な部分を取り除く方法を採ってきた。この除去工程で大半の材料を無駄にしていた。これに対してシステム・オン・フィルムでは必要な個所にのみ材料を塗るため,無駄がほとんどない。
さらに,ロール・ツー・ロールによる製造プロセスは,既存のガラスやSiを基板とする製造プロセスでは使うことができないものである。ロール・ツー・ロールでは,数百m~数kmといった長いロール状フィルムを,一列に並べた製造装置に送り込み,連続的に生産する。LSIやディスプレイなどの電子デバイスの工場の姿が,激変することになる。