エア漏れ問題は意外に根が深い?
ここは、お盆時期の某包装資材工場。生産管理担当者である佐藤さんが、忘れ物を取りに工場に戻った。すると、休転中の工場内では、ごく一部のユーティリティ設備を除いて設備の運転を停止しているにも関わらず、コンプレッサーの負荷が50%にも達しているのを見つけた。「終わりなきコスト削減策に苦心する中、どうしてこんな、瑣末な無駄が、いとも簡単に起こりうるのだろうか」と、佐藤さんは頭を抱えた。
エア漏れ対策を含むエア消費最適化に本格的にテコ入れしようという企画は、何年も前から浮上はしている。しかし、なかなか抜本的な改善に着手できず、場当たり的な対応を重ねてきた事に改めて気づかされるのだった。
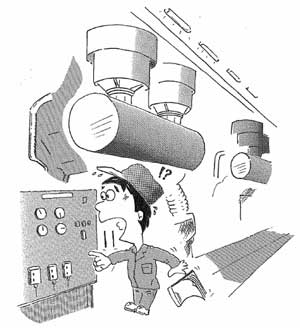
エア漏れは、比較的瑣末ですぐに解決できる問題だという認識が一般的。だが、抜本的な問題解決は意外に難しいケースが多い。
事象のくくりで個別に観察すれば、継ぎ手やねじ込み部のゆるみ、ホースの割れ、パージ用エアの出しっ放しなど、現象は様々である。なかには撤去したラインに関係する小配管が吹きっ放しだったというケースすらあった。一方、高効率コンプレッサーの普及、流量計を使った管理システム、超音波式の漏洩探査装置など、当たり前の対策方法はいくらでもある。TPM活動などをはじめ、現場における自主保全や目標管理活動もたいていの工場で行われている。
このように、改善の手段や技術は進歩している。それでも、エア消費の最適化が進まないのはなぜか。実は、エア漏れに代表される「表面的な問題」の背景には、事業の経緯・環境、管理レベルの問題までをも含んだ根深い事情をはらんでいる。この問題構造・本質を理解しなければ、事件の一気解決は難しい。エア漏れごとき! と考えると場当たり的な解決にしかならない。エア漏れは、大きな問題の氷山の一角。軽視してはいけない。「組織的犯罪」としての捜査が必要なのだ。